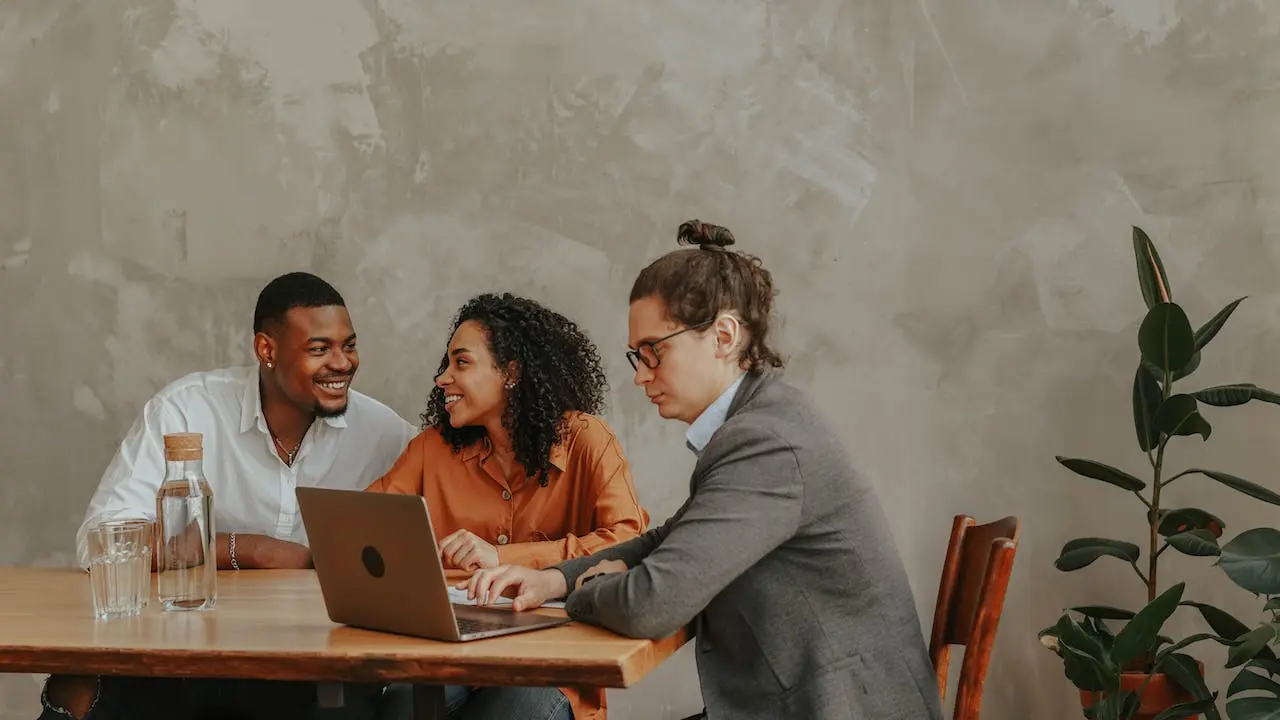
HB Fuller (NYSE: FUL), the largest pure-play adhesives company in the world, today announced that its manufacturing sites in Lüneburg and Nienburg, Germany, have achieved International Sustainability and Carbon (ISCC PLUS) certification Certification). This underlines the company’s commitment to a more sustainable future and compliance with international standards at all stages of the supply chain.
ISCC PLUS certification, one of the world’s largest independent sustainability certification systems, covers all sustainable raw materials, including biomass, circular materials and renewable energy, as well as the mass balance approach , a calculation-based method that measures the inputs and outputs of mass within of a system or a process. As defined by ISCC PLUS, this method calculates the use of sustainable materials, meaning that every operational unit in the supply chain is ISCC certified to ensure traceability.
“By continually looking for ways to reduce our carbon footprint and adopting new approaches such as: “We can now offer more solutions with verified, traceable, bio-based and recycled raw materials throughout the supply chain,” said Nathalie Ruelle, director of global quality and sustainability at HB Fuller. “HB Fuller is on track to facilitate the gradual transition to alternative materials and reduce emissions while helping our customers achieve their own sustainability goals.”
HB Fuller’s manufacturing facility in Lüneburg, Germany, has been certified as a mass balance approach compounding site and is currently using this method to produce Advantra® Earthic™ 9370 , a near carbon neutral adhesive used in e-commerce, food, personal care – and household packaging industry. This product invests in a high proportion of sustainable and biocyclable raw materials via mass balance while ensuring excellent performance.
HB Fuller’s manufacturing facility in Nienburg, Germany, has been certified as a specialty chemicals plant. Three of the core adhesives produced at this location – Rakoll® 5010, 5016 and 4020 – partially replace fossil raw materials with biologically produced raw materials produced using the mass balance approach. Not only does this reduce CO2 emissions , but it also has the potential to expand to other manufacturing processes and products, such as: B. Textiles and automobiles.