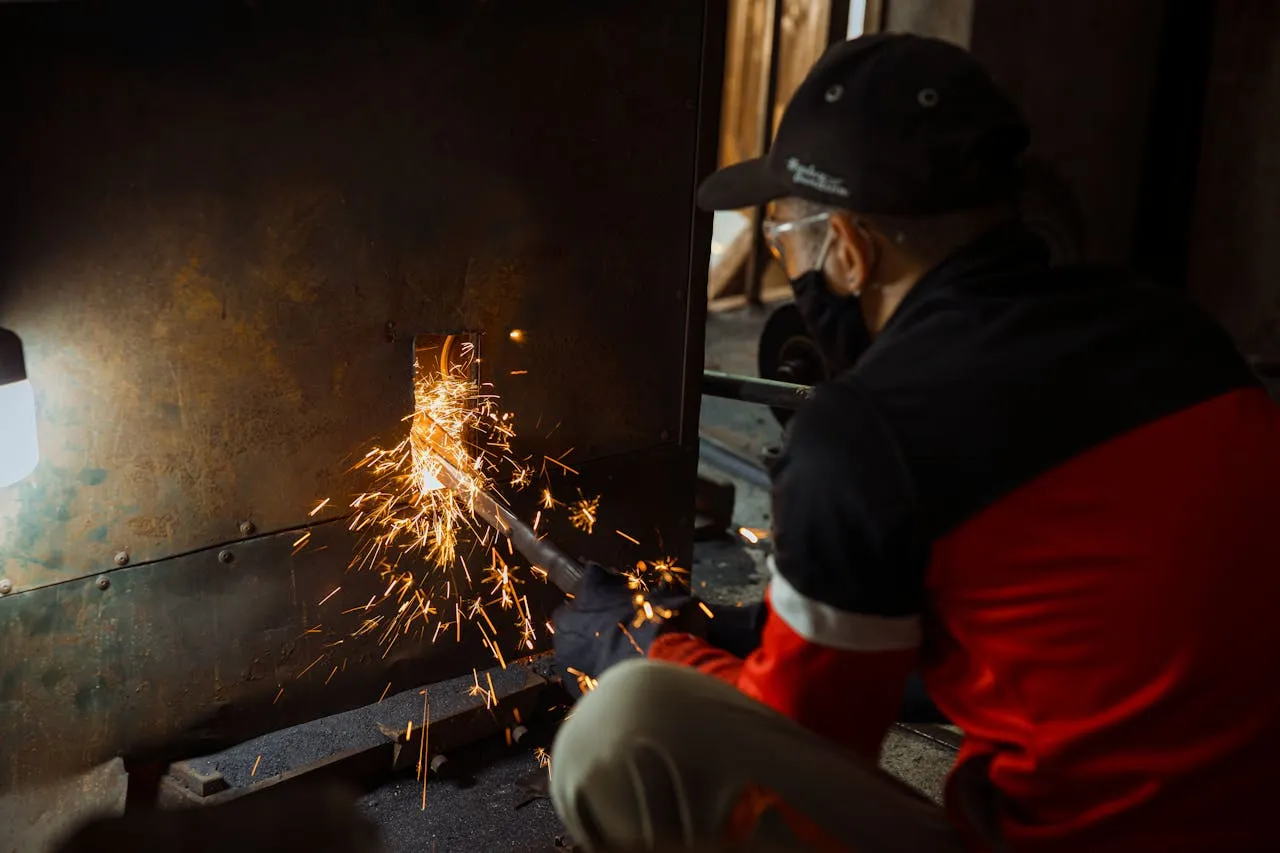
Panasonic Connect North America has launched the Syncora Digital Manufacturing Platform (SyncoraDMP), an advanced manufacturing execution system (MES) designed to expedite the digital transformation of electric vehicle (EV) battery production in the U.S. SyncoraDMP is modular, scalable, and adaptable, enabling manufacturers to meet the evolving demands of EV battery manufacturing. With features such as comprehensive traceability, quality management, process monitoring, and advanced analytics, manufacturers can optimize production for greater efficiency and faster delivery.
As demand for EV battery production surges, manufacturers face mounting pressure to enhance efficiency, ensure product quality, and adhere to changing regulatory standards. Production losses in large facilities can lead to significant financial setbacks. To succeed, manufacturers need reliable partners with extensive industry expertise and advanced technology solutions that streamline the entire process—from material receipt to final inspection and packaging.
“Being both a battery manufacturer and MES software developer, Panasonic Connect is uniquely positioned to provide end-to-end process execution in the evolving manufacturing landscape,” says Eric Symon, Head of Sales for Smart Manufacturing at Panasonic Connect North America. “Our SyncoraDMP solution integrates industry best practices, helping manufacturers avoid common challenges and achieve peak performance. By uniting machines, people, and processes, SyncoraDMP accelerates digital transformation and equips manufacturers to seize a generational production opportunity.”
Key Features of SyncoraDMP:
- End-to-End Process Orchestration: SyncoraDMP enables automatic tracking and control of the entire production process. It integrates seamlessly with upstream enterprise systems such as enterprise resource planning (ERP) and product lifecycle management (PLM), as well as supervisory control and data acquisition (SCADA) and machine-level data for enhanced monitoring and control, thereby improving product quality and minimizing returns.
- Automated Workflows: The platform utilizes advanced automation technology to identify and address defects throughout the production process, enhancing product quality and reliability. With real-time visibility and predictive intelligence, manufacturers can optimize machine usage, materials, and workflows without incurring additional costs, promoting continuous improvements with actionable insights. This also allows workers to focus on more value-added tasks.
- Flexible Deployment Options: SyncoraDMP offers modern data management applications and flexible deployment choices, including on-premise, cloud, or hybrid options. This flexibility helps manufacturers navigate scaling, configuration, and integration challenges associated with legacy systems, ensuring compatibility without concerns. The platform also supports code-free and low-code implementations for quicker return on investment.
- Real-Time Visibility: With digital twin technology, SyncoraDMP enhances overall equipment effectiveness (OEE). Access to real-time dashboards provides insights into costs related to materials, labor, downtime, and machine health, enabling proactive planning, scheduling, and maintenance to optimize factory capacity and reduce delays and waste.
- Industry-Specific Manufacturing Modeling: Given the complexity and precision required in EV battery manufacturing—such as mixing, electrode coating, and cell formation—SyncoraDMP ensures all production steps adhere to stringent quality standards without delay, prioritizing accurate and rapid modeling.
With over 100 years of experience in engineering smart enterprise solutions and more than 30 years of expertise in technology aimed at reducing waste and boosting productivity, Panasonic is well-equipped to support manufacturers in optimizing their operations.
To learn more about why SyncoraDMP is the ideal choice for EV battery manufacturers, visit: SyncoraDMP.