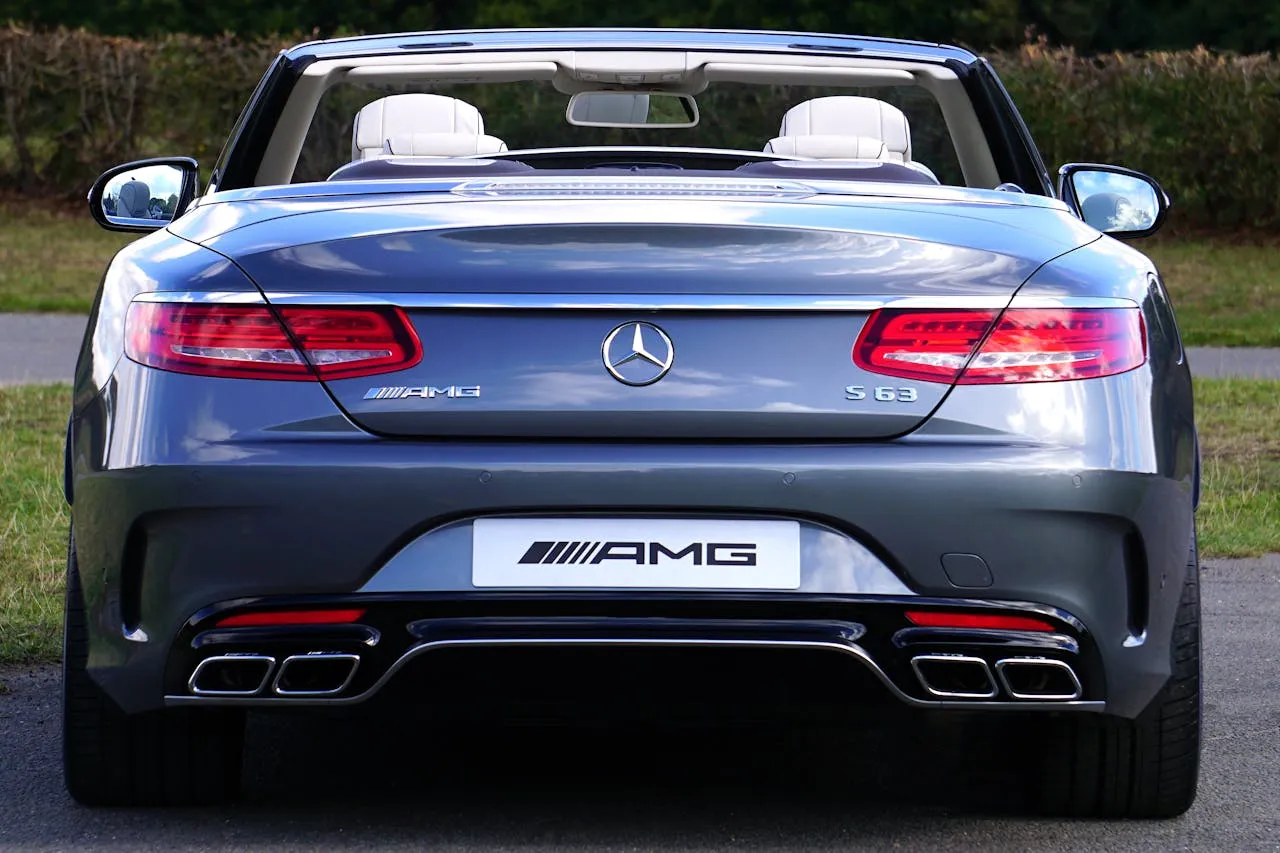
Mercedes-Benz Wörth Plant Introduces Innovative Paint Process to Cut CO₂ Emissions
The Mercedes-Benz plant in Wörth is undergoing a significant transformation to improve sustainability and reduce its environmental footprint. One of the most impactful changes is the introduction of a new and highly efficient painting process for truck cabs. This innovative approach is set to enhance the CO₂ balance of production by significantly cutting down on energy consumption and reducing material waste. Given that painting is one of the most energy-intensive steps in vehicle manufacturing, the shift to this new process marks a major step forward in the company’s commitment to sustainability.
A New Era in Truck Cab Painting
Traditionally, painting has been a resource-heavy process, requiring multiple layers, extensive drying time, and large amounts of energy. However, the new cab painting process at the Wörth plant represents a leap in production technology, designed to enhance efficiency while making a positive impact on the environment. Mercedes-Benz Trucks estimates that up to 40 percent of energy consumption in painting can be saved due to this modernization.
Andreas Bachhofer, Head of the Wörth site and Mercedes-Benz Trucks Production, highlighted the significance of this transition. “We have succeeded in developing and implementing one of the most innovative painting processes in the world at the Wörth site. In addition to the conversion of our assembly lines for the production of vehicles with alternative drive systems, the new cab painting process is one of the biggest changes for our production. We are investing substantially in the site in the next few years and are setting an important component for the future production of the largest Mercedes-Benz truck plant.”
Efficiency Gains with Ultra-High-Solid Paint Materials
One of the key factors enabling this revolutionary shift is the introduction of ultra-high-solid paint materials. These materials allow for a more streamlined painting process, offering a “wet-on-wet” application method. This means that multiple coats of paint can be applied sequentially without the need for intermediate drying steps, drastically reducing energy demand. Previously, truck cabs had to undergo drying between each layer of paint, requiring extensive energy usage from heating systems, often powered by fossil fuels.
The new process condenses the entire painting operation into a single paint box, reducing the need for multiple stations. The overall setup is significantly leaner, requiring less equipment, less space, and ultimately, less energy. The improved system is also more precise in paint application, which minimizes material waste and optimizes paint usage efficiency.
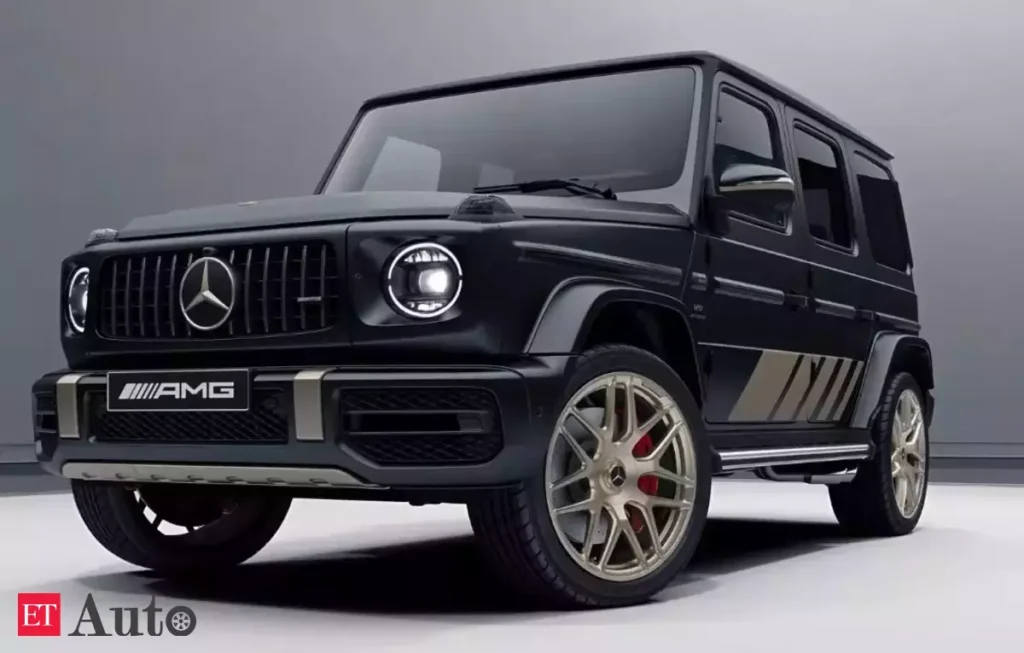
Reduction in Infrastructure and Energy Consumption
Before this change, the painting process required 15 separate stations, each contributing to high energy demands and operational costs. The new method consolidates these stations, replacing them with just five energy-efficient painting boxes and two dryers. This reconfiguration translates into substantial reductions in space requirements and operational complexity. More importantly, the drying process in the new system is entirely fossil fuel-free, eliminating a major source of carbon emissions from the plant’s operations.
Phased Implementation Without Production Interruptions
The shift to this new painting method is being carried out in phases to ensure continuous truck production. The transition began with the installation of a single new paint booth, with additional upgrades planned over the coming years. The complete overhaul of the painting process is expected to be finalized by 2026. Despite these extensive changes, the Wörth plant continues to maintain its production capacity, manufacturing over 400 truck cabs per day to Mercedes-Benz Trucks’ exacting quality standards.
Following the painting process, truck cabs proceed to the interior fitting stage before being assembled onto the chassis, a crucial step in production often referred to as the “marriage” of the truck.
Commitment to Sustainable Manufacturing Practices
The introduction of this innovative painting technology is just one of many measures Mercedes-Benz Trucks is taking to achieve its ambitious environmental goals. The Wörth plant has been operating as a carbon-neutral facility since 2022, aligning with the company’s broader sustainability strategy. This status has been achieved through the use of renewable energy sources, including solar, wind, and hydroelectric power.
Additionally, the Wörth plant is actively expanding its on-site renewable energy capabilities. Photovoltaic (solar) installations are being scaled up to enhance the plant’s self-sufficiency in green energy. A further significant initiative is the plant’s participation in the joint venture WärmeWerk Wörth, which is exploring the potential of geothermal energy for sustainable heat supply. If successful, this initiative could provide a long-term, climate-neutral energy source for the plant and surrounding facilities.
A Model for the Future of Automotive Production
The improvements at the Wörth plant exemplify how advanced manufacturing technology can drive environmental responsibility while enhancing production efficiency. By investing in cleaner and more sustainable production techniques, Mercedes-Benz Trucks is reinforcing its commitment to green manufacturing, setting a benchmark for the broader industry.
The automotive industry, particularly in the commercial vehicle sector, is facing increasing pressure to adopt more sustainable practices. Regulatory requirements, customer expectations, and global climate initiatives all demand a shift toward lower-emission production processes. Mercedes-Benz’s latest initiatives position it as a leader in this transition, demonstrating how large-scale manufacturing can reduce its environmental footprint without compromising productivity or quality.
Looking Ahead: The Future of Green Manufacturing
As the automotive sector continues to evolve, the integration of sustainable production technologies will become increasingly important. The advancements at the Wörth plant signal the beginning of a broader industry-wide transformation, where efficiency, sustainability, and innovation converge to create cleaner, more responsible manufacturing systems.
By 2026, once the full transition to the new painting process is complete, Mercedes-Benz Trucks will have significantly reduced its overall energy consumption, cutting CO₂ emissions and setting new standards in industrial sustainability. These efforts align with global climate goals and reinforce the company’s role as an industry leader in sustainable innovation.
Ultimately, the Wörth plant’s transformation highlights the potential of modern engineering and environmentally conscious design in shaping the future of truck manufacturing. As other companies look to follow suit, Mercedes-Benz Trucks’ pioneering approach will likely serve as a blueprint for the next generation of sustainable production practices in the automotive world.