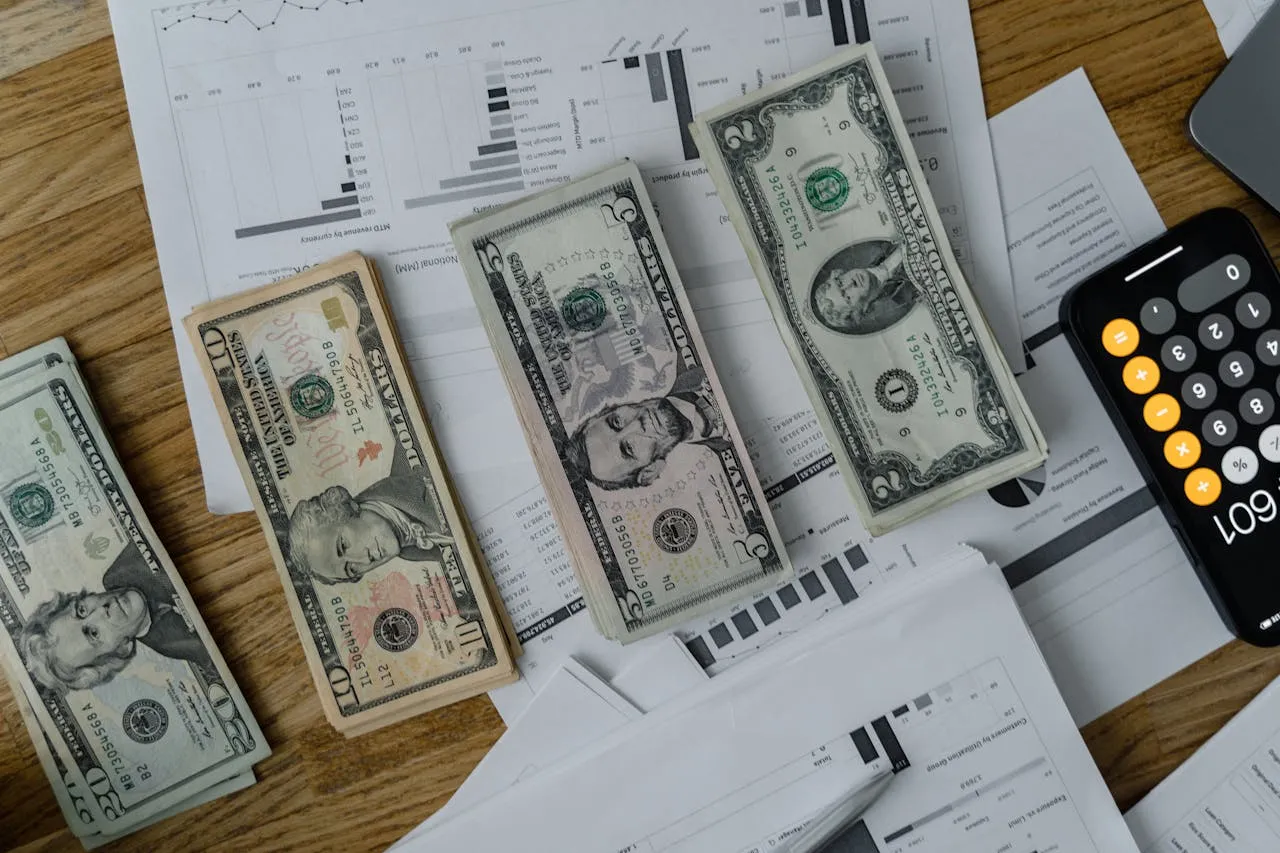
Mann+Hummel Cuts $160K Annually, Clears Six-Month Backlog, and Secures $300K Utility Rebate with Comprehensive Compressed Air System Overhaul
For most manufacturers, compressed air is as vital as electricity, gas, or water. Dubbed the “fourth utility,” compressed air powers a vast array of production equipment and tools—from pneumatic systems and assembly lines to product integrity testing stations. Yet, despite its critical role, compressed air systems are often under-optimized, neglected until they become a source of downtime, inefficiency, and spiraling costs.
That was the case at Mann+Hummel, a global leader in filtration solutions, with a major production facility struggling under the weight of recurring compressed air failures. The result was mounting inefficiencies, rising maintenance costs, and a growing backlog of customer orders.
Faced with these compounding issues, Mann+Hummel took action. In partnership with Pattons, a trusted distributor of compressed air systems and an ELGi North America company, the manufacturer embarked on a comprehensive compressed air system overhaul. The results were dramatic and far-reaching: an estimated $160,000 in annual cost savings, over 2 million kilowatt-hours in electricity savings each year, the elimination of 20 daily downtime incidents, and a restored ability to meet production targets by clearing a six-month product backlog. On top of that, the project qualified for a substantial $300,000 rebate from Duke Energy, the regional utility provider.
“It was like we had a brand-new plant,” said Steven Owens, Senior Manager of Manufacturing Engineering at Mann+Hummel. “Every day, production would stall, maintenance teams would scramble to fix issues, and we were losing money with every minute of downtime. Once the new system came online, it was like flipping a switch—suddenly, everything just worked. For the first time in years, we had stable, reliable compressed air across the entire plant.”
A Hidden Source of Operational Inefficiency
Before the upgrade, the facility’s compressed air system was a silent contributor to many of the plant’s operational issues. The infrastructure was aging, and system inefficiencies were taking a toll on product quality, uptime, and throughput.
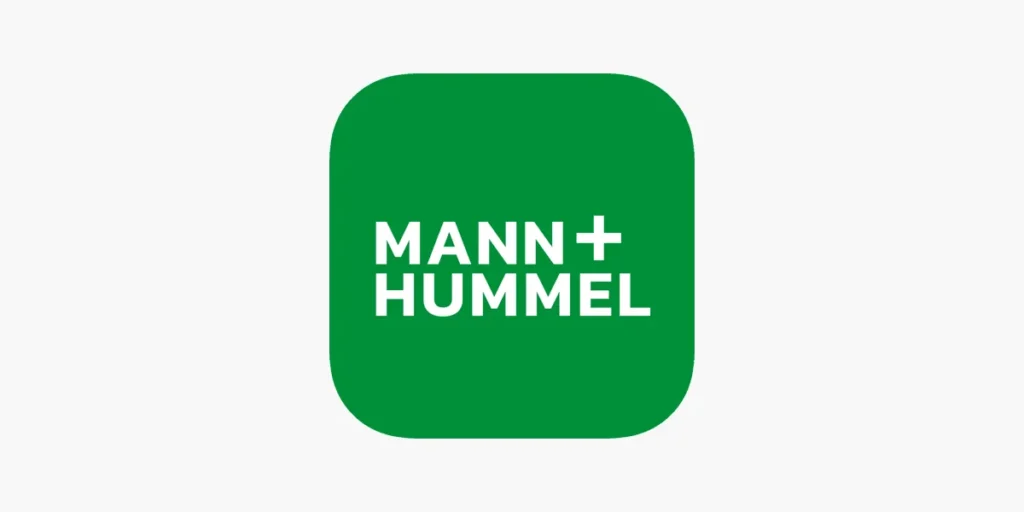
One of the most serious problems was moisture contamination. As much as 30 gallons of water per hour were entering the compressed air system, wreaking havoc on pneumatic components, including seals, valves, cylinders, and tools. This moisture not only accelerated wear and tear but also led to misalignment in assembly processes and a higher rate of product defects.
In addition to equipment degradation, inconsistent air pressure was compromising quality control. Filtration components produced at the plant rely on compressed air-driven integrity tests, which require stable, consistent air pressure. The old system’s fluctuations caused false failures and, worse, allowed undetected leaks to slip through quality inspections. As a result, filters failed to meet performance specifications, leading to increased customer complaints and a growing volume of remanufactured or scrapped products.
“We had clogged systems, defective filters, and increased quality complaints,” Owens explained. “Our products weren’t meeting the standards we needed. After the upgrade, those issues disappeared. We finally had consistent air quality, and that translated into a more consistent, higher-quality product.”
Engineering a Complete System Overhaul
To address the systemic challenges, Pattons designed and implemented a turnkey compressed air system replacement, using high-performance components from ELGi. The new system included:
- Five ELGi EG-160 rotary screw air compressors, known for their energy efficiency and long-term reliability.
- Three ELGi AR-2350 refrigerated air dryers, critical to removing moisture from the air stream and protecting downstream components.
- An Airmate Air Receiver, which helps normalize air pressure and moisture content while improving system responsiveness.
- Airmatics Smart Control System, enabling real-time monitoring and adaptive control to reduce energy consumption and stabilize output.
With the new infrastructure in place, compressed air delivery across the plant was immediately transformed. Moisture levels plummeted, pressure stabilized, and uptime soared. The days of scrambling maintenance crews and restarting stalled production lines were over.
These operational improvements unlocked significant downstream benefits. With reliable systems in place, Mann+Hummel ramped up production to address a massive backlog that had ballooned to 6 million units. Within a short time, the plant was back on schedule and operating at a level of consistency that had eluded it for years.
“For a lot of customers, filtration products are mission-critical,” Owens noted. “Delays can significantly affect automotive, industrial, and energy operations. Keeping our equipment running consistently was the key to clearing the backlog, and the air compression overhaul made it possible. It’s hard to overstate how big of a change this was—it didn’t just improve efficiency; it completely transformed how we operate.”
A Strategic Energy Play: Unlocking Utility Rebates
Beyond performance improvements, the project also delivered significant energy savings. The new air compressors and smart control system significantly reduced electricity use, eliminating over 2 million kilowatt-hours of energy demand annually. That efficiency opened the door to substantial financial incentives.
Pattons worked closely with Mann+Hummel and energy provider Duke Energy to pursue a performance-based rebate through Duke’s energy efficiency incentive program. The process required extensive documentation, including technical validation of compressor performance, load reduction data, and energy modeling for system efficiency improvements.
“We didn’t just take the easy route and accept the flat rebate,” said Trey Carter, Systems Specialist at Pattons. “We really got into the details, making sure every bit of savings was captured. In the end, we squeezed everything we could out of this project, and it paid off.”
That extra effort culminated in a $300,000 rebate—funds that helped offset the investment in new equipment and validated the company’s strategic focus on energy efficiency and sustainability.
The Bigger Picture: Sustainability and Resilience
For Mann+Hummel, the benefits of this overhaul extend far beyond cost savings and operational improvements. The project aligns with the company’s broader sustainability goals, which emphasize responsible resource use, energy reduction, and long-term operational resilience.
In today’s manufacturing environment, where supply chain delays, energy costs, and environmental regulations continue to challenge operations, investments in efficiency and reliability are not just a good idea—they’re a competitive necessity.
About the Partners
Mann+Hummel is one of the world’s premier developers and manufacturers of filtration and separation technologies, serving customers in industries ranging from automotive and agriculture to pharmaceuticals and electronics. The Mann+Hummel company’s mission is to create cleaner mobility, air, and water through innovative filtration solutions.
Pattons, a subsidiary of ELGi North America, has been providing industrial compressed air systems and services since 1945. The company specializes in complete compressed air solutions, from installation and maintenance to system audits and energy optimization. Its close partnership with ELGi gives it access to a globally respected product line of industrial air compressors and dryers, tailored to meet the demands of high-performance manufacturing environments.
As manufacturers face increasing pressure to modernize operations, improve Mann+Hummel sustainability, and reduce costs, Mann+Hummel’s story offers a compelling case study in what’s possible when core utility systems are addressed strategically.
The compressed air overhaul—while initially focused on resolving downtime and quality issues—ultimately became a springboard for Mann+Hummel broader transformation. By tackling an often-overlooked aspect of manufacturing infrastructure, the company not only improved operations but also created new capacity, resilience, and cost control that will pay dividends for years to come.