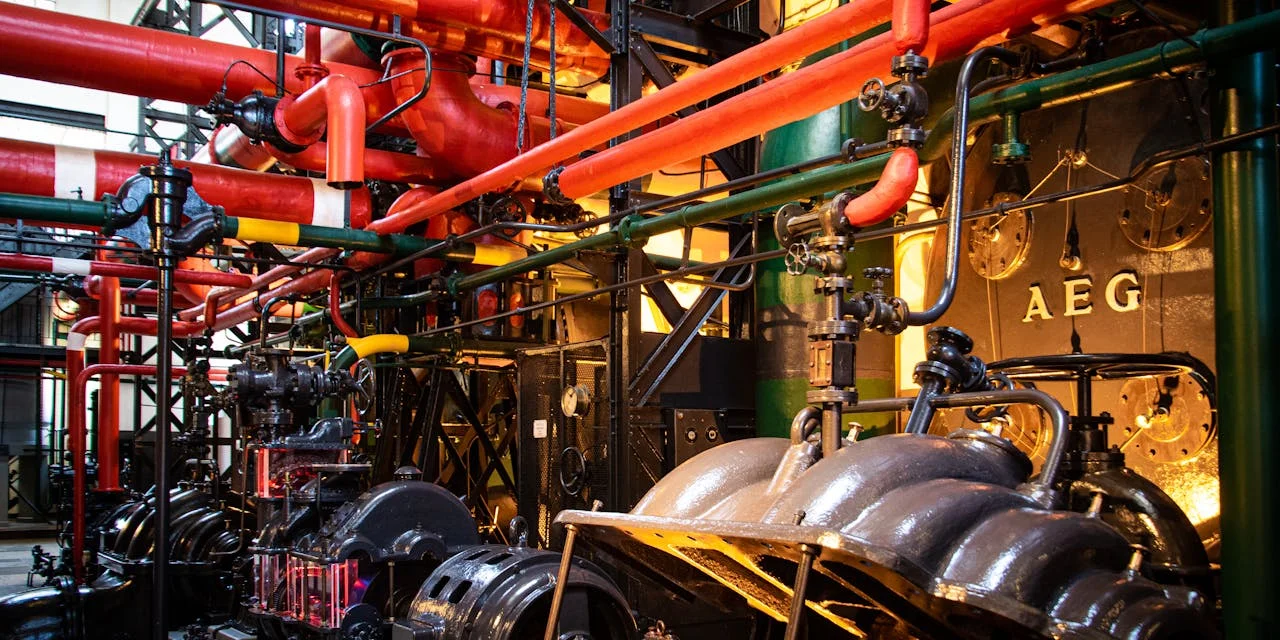
Fairbanks Morse Defense’s Hunt Valve Secures Contract to 3D Print Submarine Valve Assembly Hunt Valve, a division of Fairbanks Morse Defense (FMD), has won a contract from the Maritime Sustainment Technology and Innovation Consortium (MSTIC) to produce a 3D printed valve assembly for U.S. Navy submarines. This marks a pioneering move in the sector, with Hunt Valve utilizing additive manufacturing to create the 70-pound valve assembly, the first of its kind to be installed on a U.S. submarine. Andrew Pfister, Vice President of Aftermarket and Product Development at Fairbanks Morse Defense, hailed the development as a significant advancement for the industry, emphasizing the superior quality and reduced lead times enabled by additive manufacturing.
Traditionally, additive manufacturing for submarine components has been limited to small parts, and applications for challenging alloys like copper-nickel have been rare due to issues such as high fall-out rates in sand-casted production. However, 3D printing offers drastically higher first-time yields, accelerating production and delivery times. Hunt Valve’s contract with MSTIC will facilitate the installation of the 3D valve on any U.S. submarine class, potentially speeding up production for the Navy fleet by up to 75%.
Collaborating with Lincoln Electric, Hunt Valve is developing the valve assemblies, with Lincoln Electric responsible for additive manufacturing of the valve body. Unlike traditional manufacturing methods, which involve subtracting material from a base, additive manufacturing builds up layers to create the final product. Once printed, the valve body is sent to Hunt Valve for assembly of the remaining components using standard methods.
This innovative approach not only promises to enhance production efficiency but also contributes to the strategic goal of bolstering the Navy’s fleet with domestically produced components. Images of the 3D-printed valve body and full assembly are available [here](insert link).