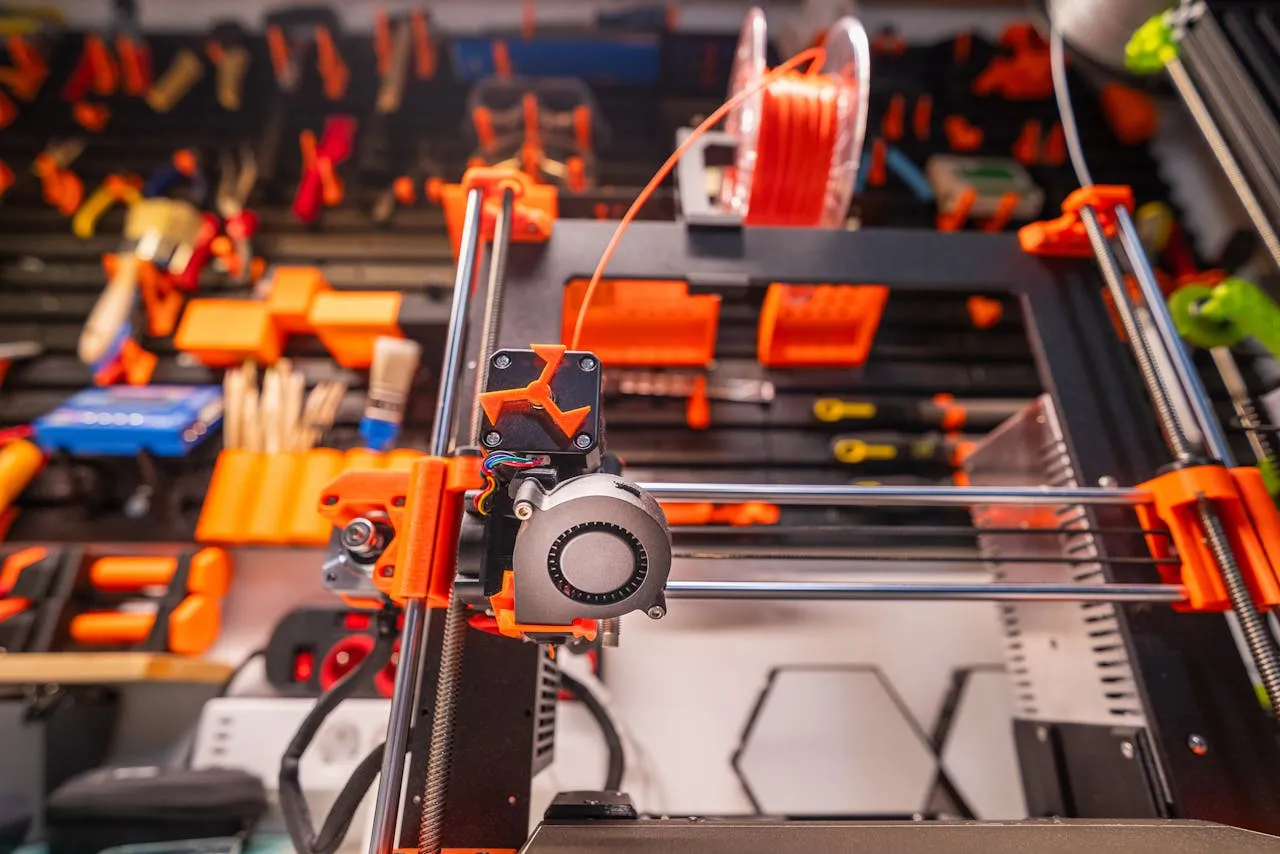
Fonon Company’s Bulk-To-Shape (BTS) additive manufacturing (AM) technology, still under development, promises to revolutionize multiple industries, including aerospace, automotive, defense, energy, maritime, nuclear, and consumer goods. This innovative technology aims to make consumer products more affordable and accessible in various ways.
One of the standout features of AM, or 3D printing, is its adaptability. Fonon’s BTS solutions can create prototypes in under 24 hours, significantly speeding up the prototyping process. This rapid turnaround reduces the time between design iterations, enabling manufacturers to bring products to market more quickly. The use of digital files facilitates easy customization, allowing products to be adjusted swiftly to meet changing consumer preferences and trends. This flexibility not only accelerates production but also lowers manufacturing costs by eliminating the need for expensive tooling, resulting in more competitive pricing.
Design freedom is another crucial advantage of Fonon’s BTS systems. Traditional manufacturing limitations will no longer pose a challenge, empowering designers to create complex and innovative components previously deemed impractical. AM has already transformed development timelines in consumer packaging, reducing them from months to days. Fonon’s accelerated design process allows for rapid prototyping and testing, with production equipment being reusable for final prototypes, further minimizing costs and time. Additionally, BTS reduces the number of parts needed, optimizing warehouse space and lowering labor costs.
Sustainability is a significant benefit of Fonon’s BTS technology. Unlike traditional manufacturing, which often generates waste by cutting down larger blocks of material, BTS printing adds layers of material, minimizing waste. Unused raw materials can be recycled into AM-grade powder. For example, shoe manufacturers have reported producing up to 60% less waste with AM. In the fuel equipment sector, companies can manufacture single-piece nozzle tips, reducing both weight and waste. By minimizing waste and energy consumption, BTS processes are not only more environmentally friendly but also more cost-effective for businesses.
Distributed manufacturing is another transformative aspect of AM. Fonon’s BTS systems can be deployed wherever needed, enabling local production that reduces transportation costs and time, thereby enhancing supply chain resilience. This allows for customized, personalized products, making small markets economically viable. This capability is particularly valuable in consumer sectors such as smart homes, IoT, wearables, and consumer electronics, where even single items can be produced affordably. The technology maximizes design flexibility, facilitating the creation of intricate geometries and innovative products without additional costs, especially beneficial in the medical and healthcare fields where custom devices are increasingly in demand.
Specific applications of AM in consumer goods include jewelry, eyewear, bicycles, beauty and cosmetics, and electronics. In jewelry, AM saves both time and costs while ensuring quality and reliability. Eyewear designers can explore new shapes and textures, producing small batches economically. Bicycle manufacturers can utilize AM to reduce costs associated with traditionally expensive materials like carbon fiber and titanium while experimenting with new designs for enhanced performance. In beauty and cosmetics, 3D printing optimizes product designs, such as mascara brushes for improved functionality. The consumer electronics sector has also seen advancements, with AM enabling the production of custom electronic enclosures featuring complex shapes, various colors, and unique graphics. High-fidelity speakers that mimic larger box speakers but are smaller and aesthetically pleasing can also be developed using AM.
In the semiconductor industry, BTS enhances the design and production of components with complex features, such as wafer tables with cooling channels and advanced kinematic couplings. This results in improved accuracy, speed, reliability, and throughput, ultimately benefiting any consumer product that relies on chips.
Fonon’s additive manufacturing solutions have the potential to significantly improve quality of life by producing prosthetics, organs, and dental devices. BTS can also enhance educational experiences through the creation of 3D miniatures for museums and cultural events, expanding cultural accessibility. As 3D printers become more affordable and user-friendly, consumers may also transition into producers.
The Fonon Company team is dedicated to offering advanced BTS 3D metal manufacturing technology to organizations seeking efficient ways to bring innovative ideas to market. BTS represents a cornerstone of Fonon’s expanding portfolio of patented and licensed technologies, next-generation hardware, and proprietary metal processing innovations. This family of specialized 3D metal printing systems is positioned as the quickest path to production readiness. For more information about Fonon Corporation’s transformative Bulk-To-Shape technology, please visit Fonon Corporation.