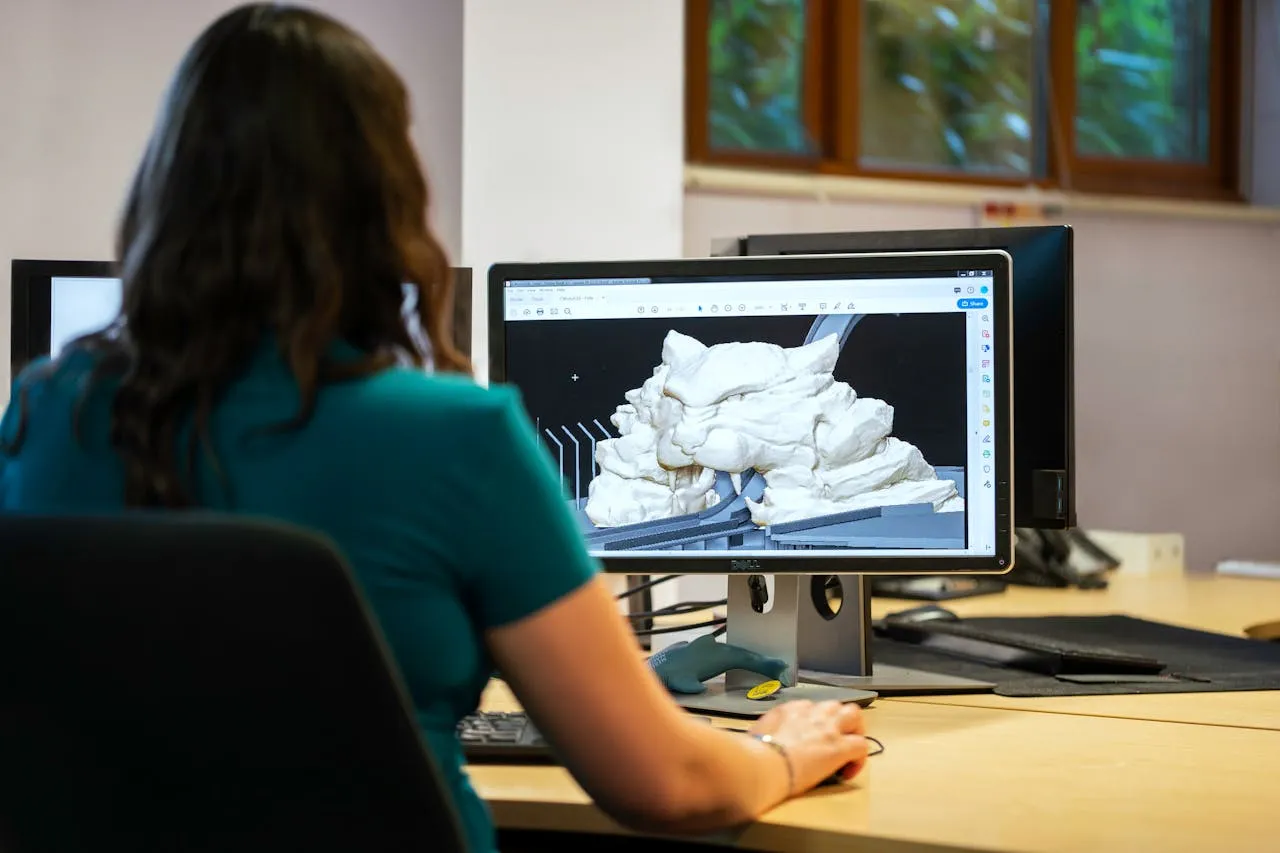
Cadillac CELESTIQ Showcases the Future of Automotive Manufacturing Through 3D-Printed Precision
For decades, General Motors (GM) has been a pioneer in advancing vehicle design and production technologies. Among these innovations, additive manufacturing—commonly known as 3D printing—has played a central role in reshaping how the company approaches design iteration, prototyping, and now, even vehicle production. While initially utilized for creating functional prototypes that enhanced engineering agility and reduced product development timelines, GM has taken a significant leap forward. Today, additive manufacturing is no longer just a behind-the-scenes tool—it’s front and center in the luxury craftsmanship and customization of the Cadillac CELESTIQ.
The CELESTIQ is not just a flagship for Cadillac—it’s a powerful statement of what the future of automotive production can look like. As an ultra-luxury, hand-built electric vehicle, the CELESTIQ is designed to redefine American automotive prestige. The vehicle incorporates over 130 components that are produced using additive manufacturing, more than any GM production vehicle to date. These parts are not simply decorative; they are functional, structural, and in some cases, safety-critical—demonstrating the robustness and versatility of 3D printing in modern manufacturing.
A New Era in Manufacturing
The automotive industry has long relied on traditional manufacturing processes like casting, stamping, and machining. While highly effective for high-volume production, these methods often pose constraints when it comes to producing intricate designs, lightweight structures, or highly customized components. Additive manufacturing, by contrast, allows engineers and designers to push the boundaries of creativity and function, fabricating parts with geometries previously deemed impossible. For CELESTIQ, this flexibility was not a luxury—it was a necessity.
“This is a vehicle that’s hand-built, where almost every detail can be tailored to the buyer’s preferences,” says Brennon White, GM technical specialist for advanced manufacturing production applications. “That level of customization would be extremely difficult—if not economically unviable—using traditional processes. Additive manufacturing opens the door to limitless design freedom.”
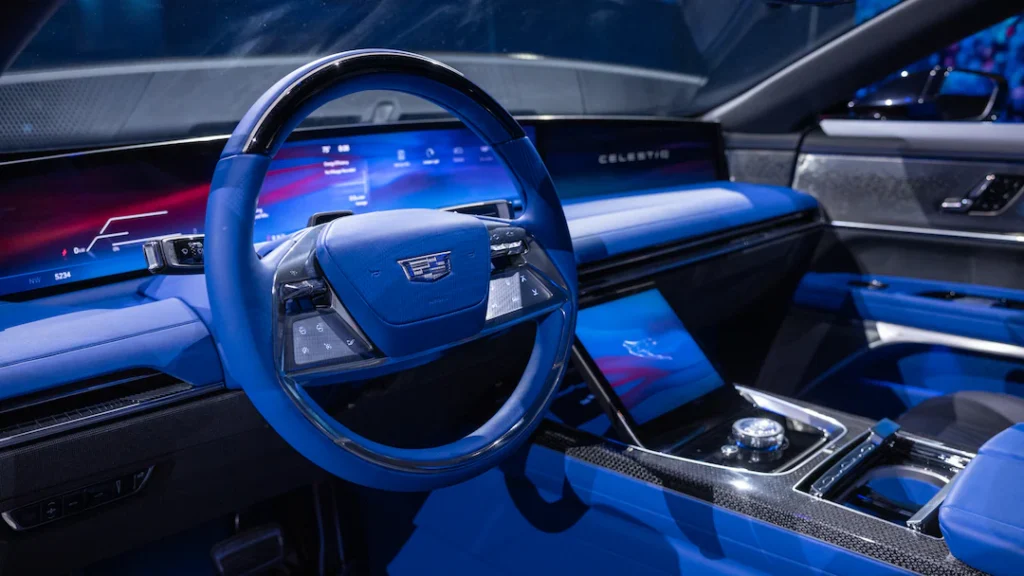
White, who has worked in additive manufacturing for more than 14 years, was heavily involved in the development of CELESTIQ’s 3D-printed components. One of the most prominent is the steering wheel center trim bezel—a part that covers the front face of the steering wheel and surrounds the switches, providing a sleek and refined aesthetic finish. This part is not only visually striking but also historic: it represents GM’s largest metal part produced through additive manufacturing for a production vehicle.
Breaking Ground with Metal Laser Powder Bed Fusion
The steering wheel trim bezel is produced using metal laser powder bed fusion (LPBF) technology. LPBF is a sophisticated 3D printing technique that involves selectively melting layers of metal powder with a high-powered laser to build solid parts, layer by layer. It’s known for its ability to produce components with high mechanical strength, excellent surface finish, and complex geometries that cannot be achieved through conventional machining or casting.
While LPBF has seen increasing adoption in aerospace and medical sectors, its use in automotive production remains relatively rare due to cost and scalability factors. However, the low-volume, high-customization nature of CELESTIQ makes it the perfect candidate. “We wanted the part to be metal to reflect the luxury character of the vehicle,” explains White. “We evaluated several manufacturing options, but additive came out on top due to its ability to deliver a compact, detailed, and elegant result.”
In addition to the steering wheel trim, CELESTIQ features a wide array of other 3D-printed components. One notable example is the seat belt adjustable guide loop—a critical safety component. This guide loop, which helps ensure proper seatbelt positioning, marks GM’s first-ever 3D-printed metal safety part. In 2024, it earned the prestigious Award of Distinction in the Automotive—Electric Vehicle category for Metal AM components from the Metal Powders Industry Federation.
White elaborates on why this part was a particularly good fit for additive manufacturing: “None of the standard finishes we explored delivered the level of sophistication and durability we needed for CELESTIQ. Additive manufacturing not only allowed us to integrate several parts into one seamless component, but also ensured strength and aesthetic integrity.”
Additive Manufacturing’s Growing Footprint Across GM
While CELESTIQ is GM’s most ambitious deployment of additive manufacturing to date, it’s not the company’s only one. Cadillac’s high-performance V-Series Blackwing models were the first production vehicles from GM to feature 3D-printed parts. These include a striking medallion on the manual transmission shifter—demonstrating how even minor design touches can benefit from additive methods. Additionally, 3D printing has become increasingly common in GM’s motorsports programs, particularly with the Cadillac Racing team, where performance, weight reduction, and part turnaround speed are critical.
At the core of GM’s additive capabilities is the Additive Industrialization Center (AIC), located on the company’s Tech Center campus in Warren, Michigan. Opened in December 2020, the AIC spans 15,000 square feet and houses more than 20 advanced additive manufacturing machines. These machines can print using a variety of materials, including both polymers and metals, enabling a broad range of applications.
According to White, the AIC plays a pivotal role in the early stages of component development. “Most of the 3D printed parts for CELESTIQ were first designed and tested here at AIC before we engaged with our supply partners for scaling and production. It gives us a sandbox to experiment with forms, fitment, and function at an accelerated pace.”
Among the 130+ additive components in CELESTIQ are parts that range from highly visible design elements—such as window switch bezels, interior grab handles, and center console décor—to structural supports hidden beneath the vehicle’s surface. Some of these parts are purely aesthetic, enhancing the cabin’s futuristic and refined look, while others perform critical functions in the structural and safety systems.
From Design Studio to Driveway: Tailoring Every Detail
What sets CELESTIQ apart, aside from its electric powertrain and luxurious materials, is the degree to which it is tailored to individual buyers. This bespoke approach harks back to the coachbuilt era of automobiles, where vehicles were customized to suit a customer’s exact tastes and preferences.
In this context, additive manufacturing becomes more than a tool—it becomes an enabler of a personalized design philosophy. Whether it’s a one-of-a-kind texture on an interior surface, a precisely tuned air vent, or a custom badge incorporating the owner’s initials, 3D printing empowers designers and engineers to meet those demands without the logistical and financial burden of traditional tooling.
“When we consider additive manufacturing for a part, we ask two key questions,” says White. “Can it meet the functional and durability requirements? And does it make sense from a cost and production standpoint? If the answer is yes to both, it becomes a strong candidate. In the case of CELESTIQ, we found ourselves answering yes again and again.”
Bridging the Gap Between Innovation and Industry
As impressive as the CELESTIQ is, it represents more than just a luxury product—it is also a proving ground for the future of manufacturing. The lessons GM learns in producing such a highly customized, low-volume vehicle will inform future projects, particularly as the industry trends toward electrification, modular platforms, and flexible production methods.
Additive manufacturing plays a key role in this shift, offering a path to reduce weight, improve energy efficiency, shorten supply chains, and eliminate excess inventory. As materials and machines continue to improve, the economics of 3D printing are becoming more favorable—not just for premium models like CELESTIQ, but for mainstream vehicles as well.
In fact, GM is already exploring opportunities to integrate additive manufacturing more broadly across its lineup. This could include underhood components optimized for weight reduction, brackets and supports with consolidated part counts, and interior elements tailored to regional market preferences. The agility and scalability of additive make it a compelling choice for an automotive world that is rapidly diversifying.
A Symbol of What’s Possible
With the CELESTIQ, Cadillac is not just resurrecting its historic moniker as the “Standard of the World”—it’s redefining what that standard means in the 21st century. This is a vehicle that doesn’t simply follow trends; it sets them. From the moment a customer begins their CELESTIQ commission, to the day the hand-built electric sedan is delivered, every step of the journey is infused with technological sophistication and craftsmanship.
Additive manufacturing is central to this vision, enabling GM to push the boundaries of design and production in ways that were previously inconceivable. It allows the company to merge the artistry of the past with the innovation of the future, delivering vehicles that are not only beautiful and functional but also a testament to what modern manufacturing can achieve.
In an era when sustainability, efficiency, and individuality are more important than ever, the Cadillac CELESTIQ stands as a powerful symbol of what’s possible when tradition meets technology. And behind the scenes, it’s the quiet hum of 3D printers—layer by meticulous layer—that’s helping bring that vision to life.