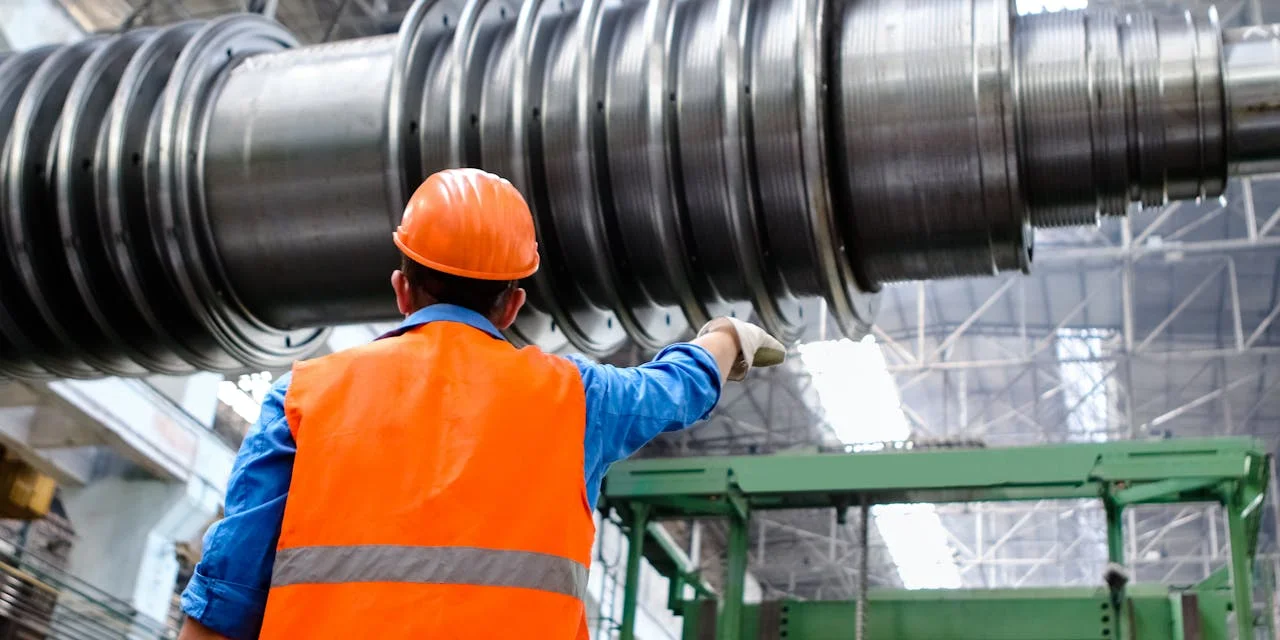
Velo3D, Inc. (NYSE: VLD) announced today that Bechtel Plant Machinery Inc. (BPMI) has chosen their fully integrated metal additive manufacturing solution to craft parts for the U.S. Naval Nuclear Propulsion Program. The selected solution includes the Sapphire XC large format printer, specifically calibrated for stainless steel 415. Operating out of a new additive manufacturing facility near Fort Lauderdale, Florida, the printer will be managed by ATI (NYSE: ATI), following a contract awarded by BPMI to ATI earlier this year. This collaboration aims to develop highly engineered part solutions, leveraging advanced manufacturing methods such as metal additive manufacturing.
The integration of Velo3D’s technology into BPMI’s operations will revolutionize the production process, particularly for mission-critical parts previously manufactured through casting. By utilizing the capabilities of the Sapphire XC printer, lead times will be significantly reduced, thereby optimizing the supply chain. Velo3D’s technology, developed in the United States, offers a fully integrated software and hardware solution, with headquarters, research and development, customer support, and manufacturing operations all based in the country.
Unlike conventional 3D printers, which often struggle with overhanging features, Velo3D’s proprietary technology allows for the production of parts with diverse geometries and minimal support structures. This capability unlocks new applications previously inaccessible to traditional 3D printing technologies. Furthermore, Velo3D’s technology enables the creation of innovative designs to replace current components, expanding the scope of possibilities.
Brad Kreger, CEO at Velo3D, praised BPMI and ATI’s forward-thinking approach to 3D printing, emphasizing the significant impact their collaborative efforts will have on enhancing the U.S. Navy’s supply chain for maintenance, repair, and operations. With approximately 300 vessels currently in operation, many of which are aging, the U.S. Navy recognizes the value of additive manufacturing in efficiently supporting its equipment and improving readiness. The partnership between BPMI, ATI, and Velo3D represents a crucial advancement in the Navy’s maintenance and operational capabilities.
Nathan Weiderspahn, BPMI Executive Manager, highlighted the importance of printers with larger build volumes and reduced support structure requirements for applications within the U.S. Naval Nuclear Propulsion Program. The additive manufacturing technology provided by Velo3D will greatly aid BPMI’s efforts in delivering innovative solutions to the Navy and ensuring the maintenance of its fleet.
Joe Thompson, General Manager of ATI Additive Manufacturing Products, expressed excitement about the enhanced capabilities offered by Velo3D’s technology, enabling the production of complex parts with fewer support structures and broader design possibilities. This advancement opens up significant business opportunities for defense and aerospace customers, facilitating higher performance and quality.
The selection of Velo3D’s Sapphire XC printer, calibrated for stainless steel 415, underscores its suitability for demanding applications. This alloy, comprising iron, chromium, and nickel, offers excellent tensile strength and corrosion resistance across various temperatures, making it an ideal choice for the stringent requirements of the U.S. Naval Nuclear Propulsion Program.