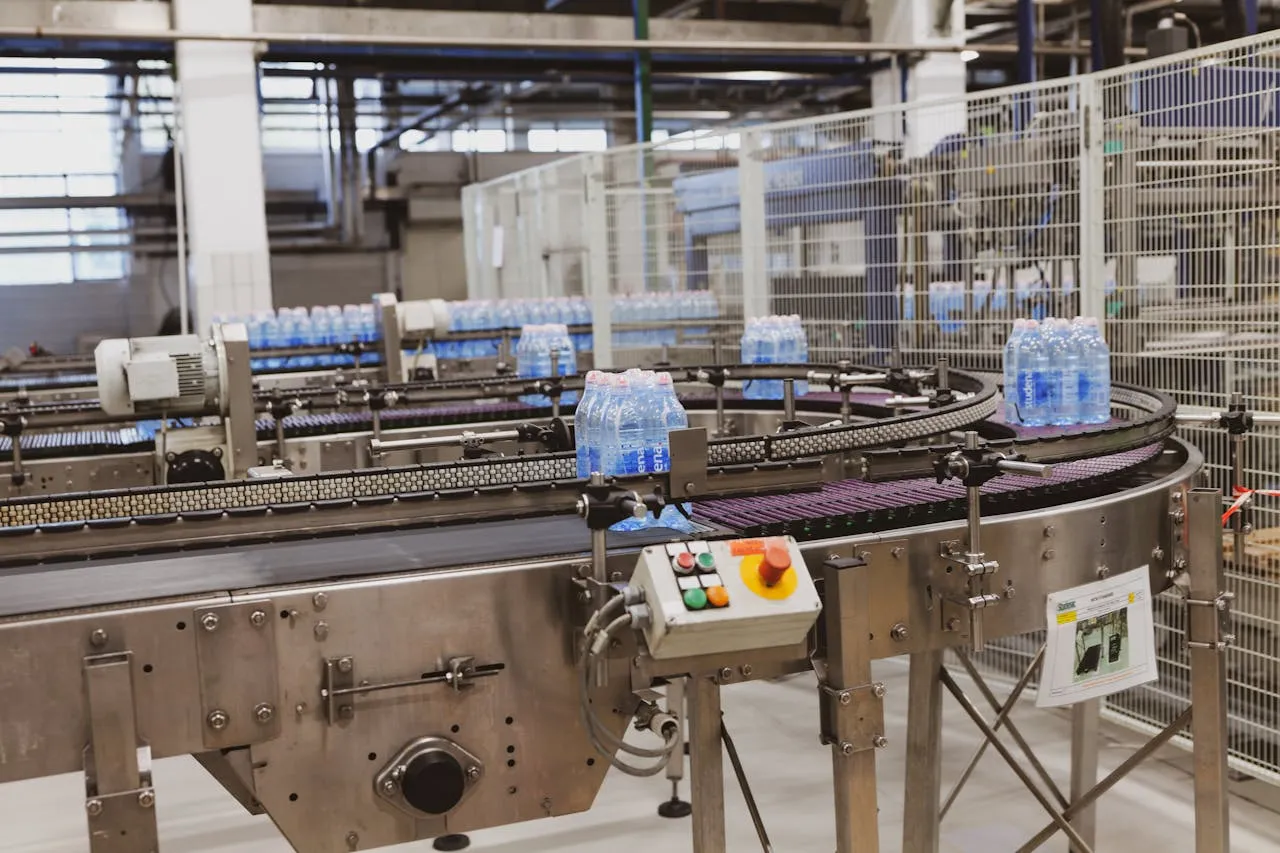
Nordson and Nordmeccanica Partner to Advance Flexible Packaging Manufacturing
Nordson and Nordmeccanica have unveiled a groundbreaking innovation poised to transform the flexible packaging industry: the Coating Weight Management (CWM) system. This fully integrated closed-loop control system introduces a new era of precision, efficiency, and ease in monitoring and managing coating weight during the converting process. By streamlining operations and addressing long-standing inefficiencies, the CWM is positioned to become an essential tool for converters worldwide.
Flexible packaging has evolved significantly in recent years. Rapid advancements in materials science, sensor technologies, and digital control systems have enabled the industry to push the boundaries of what’s possible in terms of packaging functionality and sustainability. However, with innovation has come increased cost. Stricter environmental regulations, complex material combinations, and heightened quality demands have all contributed to driving up prices. For converters, this has made every aspect of production more critical—particularly in minimizing waste, avoiding downtime, and maintaining consistent product quality.
While a variety of measurement and process control tools have been developed to address these challenges, many fall short of providing a comprehensive solution. In most cases, converters have had to juggle multiple systems that don’t integrate well, leading to inefficiencies and higher costs. What makes the CWM so revolutionary is that it brings together best-in-class hardware and software in a unified package, developed collaboratively by two industry leaders: Nordmeccanica and Nordson.
Nordmeccanica, based in Italy, is renowned for its high-performance coating and laminating machines used throughout the flexible packaging industry. Nordson, a U.S.-based technology company, is a global leader in dispensing systems and precision measurement instruments. Their collaboration marks a pivotal moment in packaging technology. It represents the first time a machine manufacturer and a sensor technology provider have directly partnered—without third-party involvement—to design a system tailored specifically to the needs of the converting industry.
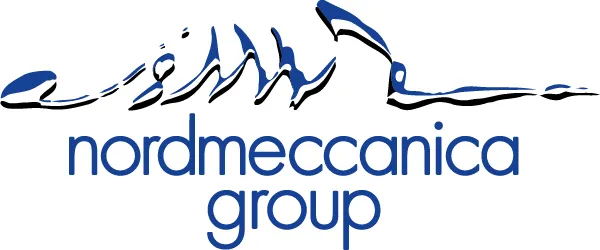
At the core of the CWM is the NM 9000 sensor, an advanced measurement device developed by Nordson. The NM 9000 leverages a unique combination of infrared optics and proprietary algorithms to deliver exceptional measurement accuracy. Designed specifically for flexible packaging applications, the sensor can detect and differentiate between three distinct chemical groups in real-time. This enables it to provide precise, continuous data on coating weight and mixing ratios, even when working with complex or multilayered substrates.
The sensor’s capabilities are further enhanced by artificial intelligence, which allows it to dynamically select the optimal measurement strategy based on the material being processed. The result is a sensor that not only collects data but actively interprets and adapts to ensure the highest levels of accuracy and efficiency. This AI-driven adaptability eliminates the need for manual recalibration between jobs, significantly reducing setup time and operator workload.
The NM 9000 is housed within Nordson’s LPS 1000 scanner—a compact, enclosed unit designed for seamless integration into Nordmeccanica’s coating and laminating lines. Its bi-directional scanning capabilities allow it to gather high-resolution data from across the web at speeds of up to 25 centimeters per second. The system achieves a baseline resolution of 512 measurement points, generating detailed, real-time profiles of coating uniformity. Importantly, the enclosed design prevents contamination from dust or debris, which is critical in maintaining measurement accuracy and system longevity.
All of this data is processed and managed by Nordmeccanica’s proprietary machine board electronics. The result is a seamless closed-loop system in which measurement data directly informs process control, automatically adjusting coating parameters to ensure optimal results. This tight integration not only boosts production efficiency but also guarantees compliance with stringent safety and quality standards. Because the CWM is managed through Nordmeccanica’s native machine interface, operators benefit from a unified control environment that simplifies training, troubleshooting, and day-to-day operations.
Another key advantage of the CWM system is its flexibility. It can be installed on new Nordmeccanica machines or retrofitted onto existing lines, allowing converters to upgrade their operations without the need for a complete equipment overhaul. The system’s single-screen interface offers both visual monitoring of coating weight and fully automated process control, enabling operators to switch between manual and closed-loop modes as needed.
From a productivity standpoint, the benefits are compelling. The CWM’s real-time feedback loop and rapid measurement capabilities drastically reduce startup times, allowing converters to bring lines up to speed faster while minimizing material waste. Additionally, by eliminating manual adjustments and guesswork, the system reduces human error and ensures consistent quality across production runs. This translates into tangible cost savings through reduced scrap, lower downtime, and enhanced product quality.
What truly sets the CWM apart, however, is its ease of use. Despite its technical sophistication, the system has been engineered with the operator in mind. Nordmeccanica’s intuitive user interface, combined with Nordson’s plug-and-play sensor technology, means that operators can quickly become proficient with minimal training. For companies grappling with labor shortages or high turnover, this ease of adoption is a critical advantage.
Furthermore, the CWM system aligns well with the broader industry trend toward digitalization and smart manufacturing. As converters seek to implement Industry 4.0 technologies, the ability to gather, analyze, and act on real-time production data is becoming a must-have capability. The CWM delivers on this front by serving as a digital backbone for the coating process, enabling more informed decision-making and continuous process improvement.
From a strategic perspective, the partnership between Nordson and Nordmeccanica signals a shift in how packaging technology will be developed moving forward. By bypassing traditional vendor relationships and working together from the ground up, the two companies have created a solution that is greater than the sum of its parts. This model of collaboration may well set a precedent for future innovation in the converting and packaging sectors.
In the words of industry observers, the CWM isn’t just a product—it’s a platform. It provides converters with the tools they need to compete in an increasingly complex and cost-sensitive market. It also demonstrates what can be achieved when engineering excellence meets customer-focused design. Rather than adding layers of complexity, the system simplifies operations while enhancing performance.
In conclusion, the launch of the Coating Weight Management system marks a major leap forward for the flexible packaging industry. Nordson and Nordmeccanica have combined their respective strengths to create a solution that addresses longstanding challenges in coating and laminating. With its advanced sensing capabilities, real-time data integration, and user-friendly interface, the CWM empowers converters to operate more efficiently, produce higher quality output, and respond more quickly to changing market demands.
As the packaging industry continues to evolve, solutions like the CWM will be essential in helping manufacturers maintain a competitive edge. Whether it’s reducing waste, lowering costs, or ensuring regulatory compliance, the CWM delivers measurable benefits that go straight to the bottom line. In a world where precision, speed, and adaptability are more important than ever, Nordson and Nordmeccanica have delivered a solution that rises to the challenge—and sets a new standard for the future.