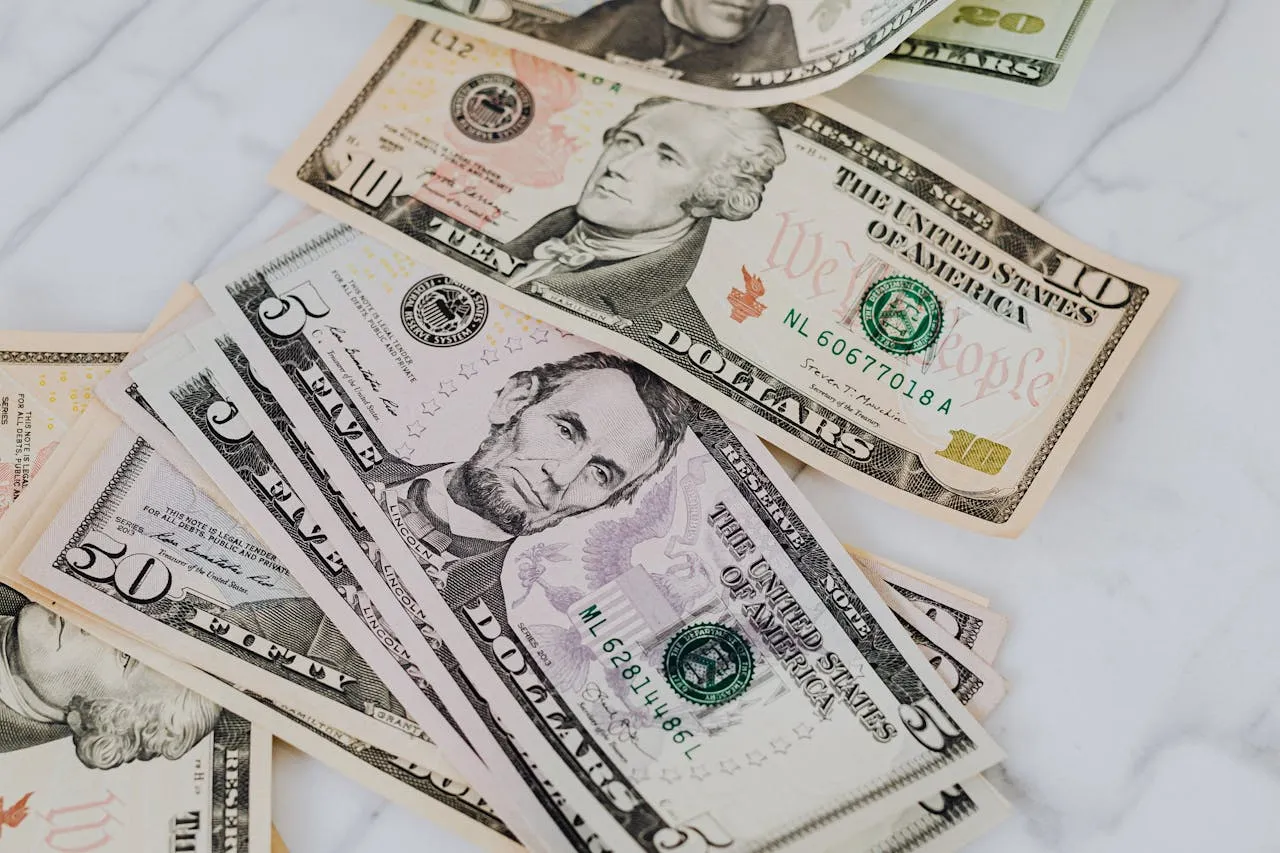
Casa Herrera’s Lean Success: Process Improvements & Cost Savings with CMTC
California Manufacturing Technology Consulting® (CMTC) recently partnered with Casa Herrera to implement a Lean/Continuous Improvement training program aimed at enhancing efficiency, reducing costs, and fostering a culture of teamwork and innovation. Established in 1951, Casa Herrera, Inc. is a leading designer and manufacturer of custom machinery for the production of corn and flour tortillas, corn and tortilla chips, tostadas, taco shells, quesadillas, burritos, pita bread, pizzas, arepas, chapatis, and other ethnic foods from around the world. Casa Herrera’s customer base ranges from large multinational corporations to single-line in-store producers.
The Need for Change
As the old adage goes, “The reward for good work is more work.” Casa Herrera’s decades of experience have earned them attention and interest across the industry. With increasing customer demand and growing complexity in operations, the company’s leadership recognized the need for external support and expertise. Their primary objectives included streamlining manufacturing processes, reducing production costs, and fostering a company-wide culture of Continuous Improvement among their dedicated, long-term employees.
Partnering with CMTC for Lean Transformation
To address these challenges, Casa Herrera collaborated with CMTC to develop a tailored Lean/Continuous Improvement training program. This program was uniquely designed to align with the company’s family-oriented workplace culture. The curriculum was project-based and facilitated by an experienced CMTC instructor. To ensure engagement and accountability, Casa Herrera employees were divided into four teams, each tasked with a specific area of responsibility and a measurable improvement goal.
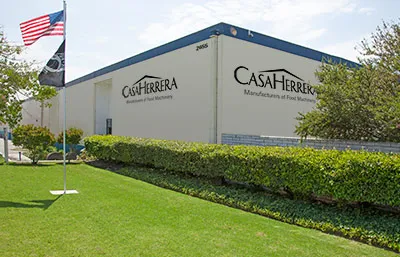
The Four Lean Improvement Teams
Each of the four teams focused on different aspects of Casa Herrera’s manufacturing operations:
- Engineering Cycle Time Reduction
- Objective: Reduce the development time required from the receipt of a customer order until engineering drawings were ready for release to the shop floor by 25%.
- Approach: This team worked on optimizing engineering workflows, improving communication between departments, and eliminating unnecessary steps in the design process.
- Stock Room Labor Cost Reduction
- Objective: Decrease the monthly labor costs associated with stock room personnel.
- Outcome: During the team’s final presentation, they demonstrated a cost reduction of 37% by implementing more efficient inventory management and material handling practices.
- Rework Reduction
- Led by Casa Herrera’s CFO, this team focused on identifying and addressing excessive rework in products and processes.
- Results: The team identified multiple products that had high levels of rework and implemented corrective measures to minimize errors and waste.
- Problem-Solvers
- Objective: Improve assembly processes in the shop to enhance efficiency and organization.
- Approach: The team began with an extensive 5S clean-up of the assembly areas, ensuring that workspaces were orderly and optimized for efficiency. They also developed a system for storing kitted parts in designated racks, reducing the time assemblers spent searching for components.
Implementing 5S and Visual Controls
By the end of the training program, all four teams successfully integrated a 5S system and visual controls within their respective areas. The 5S methodology (Sort, Set in Order, Shine, Standardize, and Sustain) played a crucial role in improving workplace organization, reducing waste, and creating a more efficient workflow. Visual controls further enhanced process transparency, allowing employees to quickly identify areas needing attention and maintain consistency in operations.
Measurable Results and Future Impact
The Lean transformation at Casa Herrera has already yielded significant results. The company estimates that it will retain all existing jobs while creating an additional 5-10 new positions within the next year. Furthermore, the training is expected to generate cost savings of 10-20%, allowing the company to reinvest in innovation and future growth.
Reflecting on the experience, Mark Herrera, President of Casa Herrera, emphasized the value of teamwork and communication: “Our CMTC instructor was outstanding! We learned many different methods of validating information and asking questions. What was big for us was working together and understanding that by working as a team and being able to communicate, we can improve.”
Strengthening Company Culture Through Continuous Improvement
Beyond cost savings and operational efficiency, the partnership between Casa Herrera and CMTC has instilled a mindset of Continuous Improvement throughout the organization. Employees at all levels are now more engaged in identifying inefficiencies, proposing solutions, and collaborating to enhance overall productivity. This cultural shift ensures that the benefits of Lean training will extend well beyond the initial implementation phase.
Casa Herrera plans to build on the success of this initiative by continuing to refine its processes and training programs. The company remains committed to leveraging Lean methodologies to stay competitive in an evolving industry. With CMTC’s guidance, Casa Herrera has not only achieved tangible process improvements but has also empowered its workforce to drive ongoing innovation and excellence.