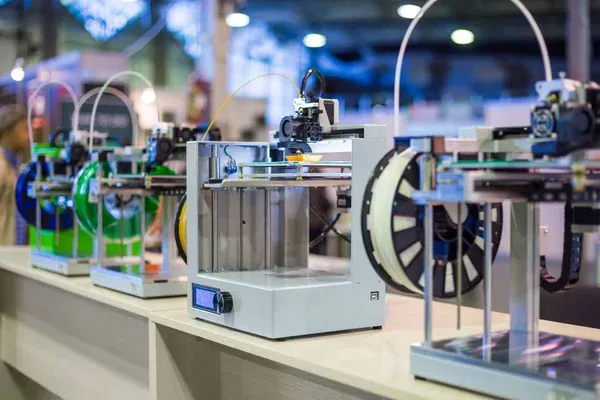
GM’s 3D Printing Drives Innovation in Products and Plants
General Motors (GM) is steadfastly dedicated to pushing the boundaries of innovation, continually seeking ways to improve efficiency, reduce costs, and enhance safety. One of the key tools in this effort is additive manufacturing, commonly referred to as 3D printing. This advanced technology has become a cornerstone in GM’s pursuit of smarter production processes and more innovative designs, revolutionizing everything from prototyping to full-scale manufacturing.
3D Additive manufacturing involves creating intricate three-dimensional components by layering material based on digital blueprints. Unlike traditional subtractive manufacturing methods, which remove material to achieve the desired shape, additive manufacturing builds parts from the ground up, enabling unparalleled precision and complexity. For over three decades, GM has been harnessing this technology across various domains, including design, product and materials engineering, vehicle manufacturing, and aftersales. The results have been transformative, with applications spanning body hardware, electrical components, interior systems, and more.
Revolutionizing Prototyping and Design
A critical area where 3D additive manufacturing has made a significant impact is the prototyping stage. GM uses this technology to create early prototypes that supplement virtual designs. By producing physical prototypes directly from digital models, the company can evaluate designs in real-world conditions, ensuring accuracy and functionality. This approach not only accelerates the development process but also reduces costs associated with traditional prototyping methods.
Moreover, the ability to iterate quickly on designs allows teams to refine products with greater precision. Virtual designs can be seamlessly translated into tangible prototypes, enabling engineers to test and validate concepts more efficiently. This 3D streamlined workflow is particularly advantageous as GM develops cutting-edge technologies for its vehicles, including those in its growing lineup of electric vehicles (EVs).
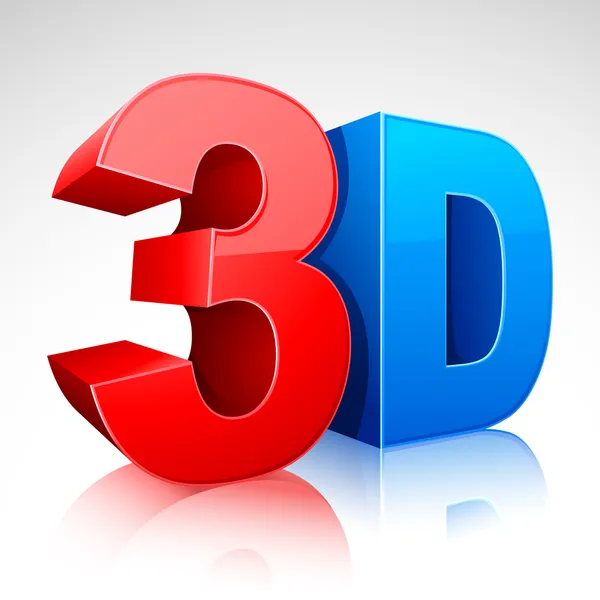
Enhancing Manufacturing Processes
3D Additive manufacturing has also revolutionized GM’s manufacturing plants by simplifying tools and fixtures. For example, GM employs this technology to create custom tools that aid assembly line workers. These tools are often more lightweight and ergonomic than their traditional counterparts, enhancing worker safety and comfort.
At the Lansing Delta Township Assembly plant, which produces the Buick Enclave, Chevrolet Traverse, and GMC Acadia, a prime example of 3D additive manufacturing’s impact can be seen. Assembly line operators previously relied on a metal fixture weighing 14 pounds to prop open vehicle hoods during assembly. This exceeded the 10-pound limit for a one-handed lift, posing ergonomic challenges. By collaborating with GM’s additive manufacturing team, the plant developed a lighter, 3D-printed alternative that not only addressed the weight issue but also improved overall efficiency.
Paul Wolcott, a GM technical specialist, highlighted the transformative potential of 3D additive manufacturing: “Additive manufacturing continues to enable us to build our vehicles safer and quicker. From accelerated lead times for tools to addressing ergonomic issues with lightweight solutions, we keep seeing growth in applications the more we implement it.”
Durable and Cost-Effective Components
Another advantage of 3D additive manufacturing lies in its ability to produce durable and cost-effective production components. By leveraging materials such as titanium and advanced polymers, GM can create parts that meet stringent performance standards while reducing material waste. This capability is particularly important as the company strives to achieve greater sustainability in its operations.
In addition to manufacturing tools and fixtures, GM also uses 3D additive manufacturing to produce end-use components for vehicles. This approach allows the company to address supply chain challenges and respond swiftly to production needs. By creating parts in-house, GM can reduce lead times and maintain tighter control over quality, ensuring that every component meets its exacting standards.
Driving Innovation Across the Board
In 2024 alone, GM executed over 5,400 new 3D additive manufacturing projects. This impressive number underscores the technology’s growing role within the company. From developing ergonomic solutions for assembly lines to creating prototypes and production components, the applications of additive manufacturing are expanding rapidly. As GM’s expertise in this field deepens, the company expects even greater innovation in 2025 and beyond.
One of the key drivers of this growth is GM’s focus on an all-electric future. As the automotive industry transitions to EVs, the demands on design and manufacturing processes are evolving. Additive manufacturing plays a crucial role in meeting these new challenges. For instance, it enables engineers to explore novel design possibilities, optimize component performance, and integrate advanced materials into vehicles. These capabilities are essential as GM works to deliver EVs that are not only environmentally friendly but also technologically advanced.
Bridging the Virtual Gap
Another area where additive manufacturing excels is in bridging the gap between virtual designs and physical production. By translating digital concepts into tangible components, the technology allows GM to address real-world challenges more effectively. This capability is especially valuable in areas such as ergonomics, where physical prototypes can be tested and refined to ensure optimal performance and safety.
For example, GM’s additive manufacturing team has developed operator assists that enhance workplace safety and efficiency. These tools are tailored to the specific needs of assembly line workers, making their tasks easier and more ergonomic. By reducing the physical strain associated with certain activities, these solutions contribute to a safer and more productive work environment.
As GM continues to integrate additive manufacturing into its operations, the company is unlocking new possibilities for innovation. The ability to create complex, high-performance components directly from digital designs is transforming the way vehicles are designed and built. This technology not only enhances GM’s manufacturing capabilities but also supports its broader goals of sustainability and electrification.
The company’s commitment to innovation is evident in its ongoing investments in additive manufacturing. By leveraging this technology, GM is poised to remain at the forefront of the automotive industry, delivering vehicles that meet the needs of today’s consumers while paving the way for a more sustainable future. Whether it’s through improving ergonomics, accelerating prototyping, or producing durable components, additive manufacturing is shaping the future of GM’s operations and products.
In conclusion, additive manufacturing represents a powerful tool in GM’s arsenal, enabling the company to innovate across its footprint. From pre-production to motorsports, this technology is driving advancements that benefit both employees and customers. As GM looks toward an all-electric future, the role of additive manufacturing will only continue to grow, helping the company achieve its vision of a safer, more efficient, and sustainable automotive industry.