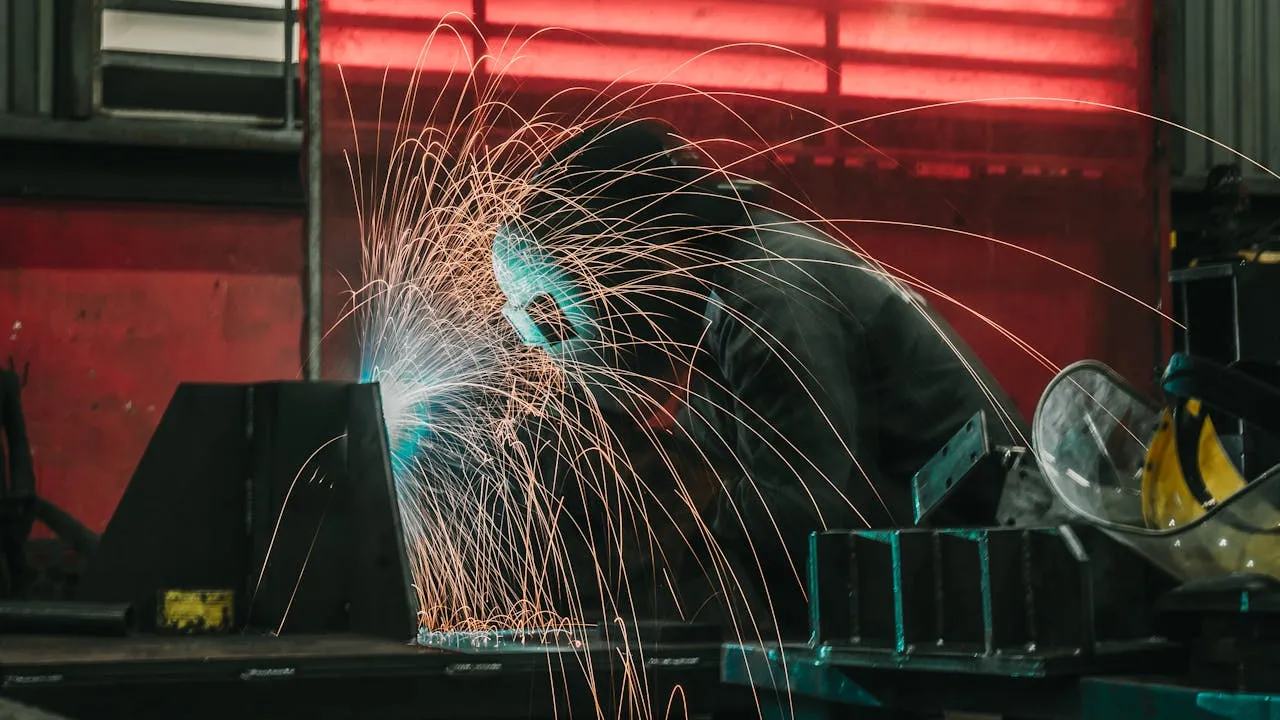
At the end of November, Mercedes-Benz Trucks will officially commence series production of the eActros 600 at its Wörth facility. Recently awarded “International Truck of the Year 2025” at the IAA Transportation in Hannover, the eActros 600 will see its first customer vehicles manufactured and registered before the close of 2024. Essential components for each vehicle will come from Mercedes-Benz’s Gaggenau and Kassel plants, marking a significant milestone in electric commercial vehicle manufacturing.
Gaggenau: A Hub for eAxle Production
Specializing in transmissions for heavy-duty vehicles, the Gaggenau plant is advancing as a key player in electric drive technology. Since 2021, Gaggenau has been producing critical components for the e-axle used in models like the eActros 300/400 and eEconic. This expertise extends to the new generation of electric axle components for the eActros 600, where the Gaggenau team will craft approximately 30 unique mechanical parts, such as shafts, gears, and synchronizers, for the innovative 4-speed axle drive.
Additionally, Gaggenau will manufacture bodyshell components for the eActros 600 cab, supplying structural parts like the rear panel, roof frame, and reinforcements. These are based on existing parts already used in conventional trucks, supporting the new electric cab’s design with the plant’s longstanding bodywork expertise.
The plant’s modern manufacturing capabilities include highly precise gear-grinding and other advanced technologies to meet the stringent quality standards required for electric powertrain components. Housing parts for these components are processed in a specially upgraded hall with new automated processing centers, reducing setup time thanks to digital twins that simulate production.
Leadership Insights from Gaggenau
Thomas Twork, Plant Manager at Gaggenau, highlights the plant’s heritage: “No future without the past! Our tradition and transformation go hand in hand. Our decades of experience in transmission manufacturing contribute significantly to the new electric powertrain.” Michael Brecht, Chairman of the Group Works Council at Daimler Truck, adds, “This production network with Kassel represents an essential step toward the new electric powertrain, guiding our workforce as we embrace new technology.”
Kassel: Excellence in E-Axle Assembly
As the global center for axle and electric drive systems, the Kassel plant is assembling the eActros 600’s next-generation e-axle. Designed for long-distance transport, the rear axle features advanced technical innovations to enhance performance and efficiency. A new assembly line at Kassel includes dedicated testing stations to ensure functional and safety standards are met, while the “common parts principle” enables Kassel to flexibly produce both conventional and electric axles.
The new e-axle comprises an axle arch, electric motors, transmission, and high-voltage components. Kassel’s assembly process follows a structured sequence, beginning with axle carrier preparation for wheel hubs, drive shafts, and brakes. The assembly of the electric drive unit then integrates Gaggenau-produced parts into the axle carrier housing. Finally, each unit undergoes an “end-of-line test” to validate the mechanical and electrical components through simulations of driving scenarios before transport to Wörth.
Leadership Insights from Kassel
Hauke Schuler, Plant Manager at Kassel, celebrates this milestone: “The e-axle’s efficient design for CO2-neutral long-distance transport reinforces the eActros 600’s range and marks a significant step toward emission-free mobility.” Jörg Lorz, Chairman of the Kassel Works Council, underscores the commitment: “Our Kassel team is passionate about contributing to this innovative drive technology, fostering collaboration with Gaggenau to drive Daimler Truck’s success.”
With key components from Gaggenau and Kassel, Mercedes-Benz Trucks is ready to set a new standard in electric trucking with the eActros 600. This collaborative production approach highlights Mercedes-Benz’s commitment to sustainable mobility and the advancement of electric vehicle technology.