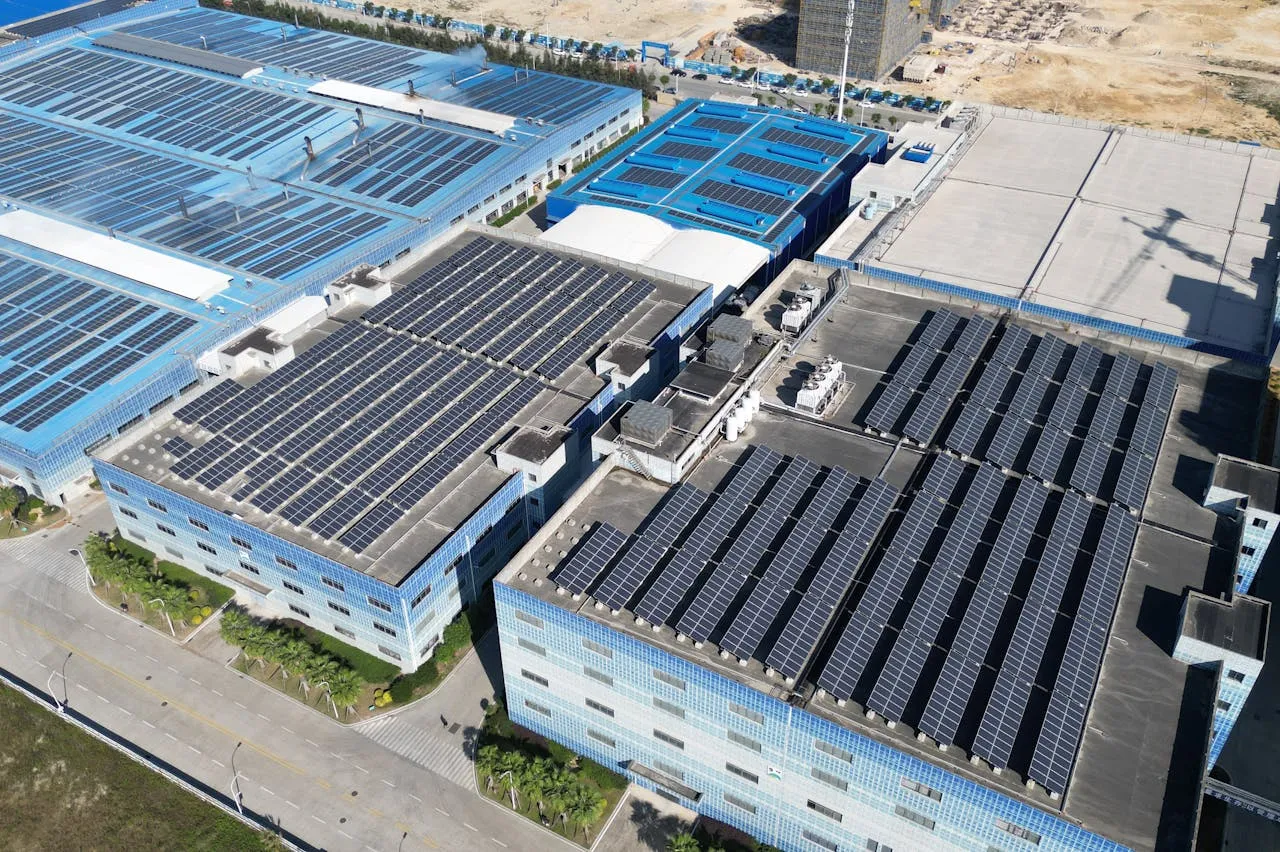
Tenaris and EPRI Strengthen Long-Standing Collaboration to Advance Steels for Modern Power Generation Plants
For more than ten years, Tenaris, a global leader in steel pipe manufacturing for the energy industry, has partnered with the Electric Power Research Institute (EPRI), a U.S.-based nonprofit organization focused on research and development related to electricity generation, delivery, and use. This long-standing collaboration is rooted in a shared vision: to push the boundaries of materials science and engineering in support of safer, more reliable, and more efficient power generation systems. Together, Tenaris and EPRI have worked on innovative approaches to developing advanced steel solutions that meet the demanding performance criteria of high-temperature and high-pressure environments found in modern power plants.
As the global energy landscape evolves with a growing emphasis on sustainability, efficiency, and long-term resilience, the need for materials that can withstand extreme conditions becomes even more critical. This is especially true for power generation facilities that rely on advanced thermal cycles and operate under increasingly stringent operational parameters. With that in mind, Tenaris and EPRI continue to deepen their technical engagement, leveraging their complementary strengths in manufacturing, metallurgy, and applied research to improve the performance of critical steel components used in turbines, boilers, and heat exchangers.
A recent milestone in this collaboration came when Tenaris hosted Dr. John Siefert, head of EPRI’s materials research group, for an extensive series of technical discussions and guided tours at two of Tenaris’s major European manufacturing facilities—its pipe mills in Dalmine, Italy, and Zalău, Romania. These facilities are among Tenaris’s strategic hubs for producing high-performance steels tailored for the power generation industry. Both locations have dedicated production lines that adhere to the most rigorous standards for producing advanced grades, including Grades 91 and 92, which are widely used in high-temperature applications within thermal power plants.
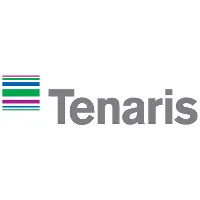
During his visit, Dr. Siefert had the opportunity to meet with Tenaris’s R&D and production teams to delve into the specifics of steelmaking processes, quality assurance protocols, and metallurgical performance testing. These technical sessions were aimed at aligning EPRI’s cutting-edge research with Tenaris’s real-world production capabilities, ensuring that future steel development efforts are both scientifically sound and industrially scalable.
“Tenaris brings a unique combination of steelmaking expertise, meticulous quality control, and advanced laboratory testing,” said Dr. Siefert. “Their work contributes significantly to developing practical industry guidelines for Grades 91 and 92, which are critical materials in high-efficiency thermal power plants due to their exceptional creep resistance and thermal stability. These properties are essential for ensuring the structural integrity of components exposed to prolonged high-temperature service.”
Creep resistance—the ability of a material to withstand long-term exposure to high stress and temperature without undergoing permanent deformation—is a key requirement for components in high-temperature steam cycles. Materials like Grade 91 (9Cr-1Mo-V-Nb) and Grade 92 (9Cr-0.5Mo-W-V-Nb) are part of a family of ferritic-martensitic steels specifically designed to provide long-term mechanical strength in such harsh environments. Over the past decade, these materials have become the industry standard for high-temperature headers, piping systems, and pressure vessels in fossil fuel and combined-cycle power plants.
Tenaris has made significant investments in its manufacturing and metallurgical capabilities to meet the unique challenges posed by these advanced steels. According to Matteo Ortolani, Technology Product Senior Manager for Power Generation at Tenaris, the company’s collaboration with EPRI has played a critical role in refining these capabilities.
“Our ongoing technical partnership with EPRI gives us access to a valuable ecosystem of shared data, experimental insights, and real-world application feedback,” Ortolani explained. “We exchange research samples, compare metallurgical data, and validate findings through rigorous testing. This gives us a deeper understanding of how different manufacturing variables—from alloy composition to heat treatment cycles—ultimately affect the mechanical performance and longevity of our steel products.”
Ortolani emphasized that Tenaris’s collaborative model with EPRI is not just about compliance with industry norms, but about actively shaping them. As many of EPRI’s materials studies inform industry standards, Tenaris’s involvement in early-stage development allows the company to influence the technical guidelines that later become essential references for power plant designers, operators, and regulators. This not only strengthens Tenaris’s credibility as a premium supplier but also positions the company at the forefront of innovation in the field of high-performance steels.
A key focus of the recent sessions was the effect of trace elements and non-metallic inclusions on steel integrity. Detailed discussions revolved around the influence of residual elements such as sulfur, boron, aluminum, and titanium on the microstructural behavior and long-term performance of the steel. While often present in minute quantities, these elements can significantly affect grain boundary strength, creep resistance, and oxidation behavior—factors that are crucial for power plant operators seeking to extend service life and minimize maintenance-related downtime.
“Even small variations in chemical composition or impurities can lead to significant differences in performance under high-temperature conditions,” said Dr. Siefert. “Understanding and controlling these variables is vital for ensuring the reliability and safety of power plant infrastructure.”
The sessions also addressed how process parameters such as forging temperatures, austenitizing cycles, and tempering practices impact the formation of microstructures that are optimized for creep strength and fracture resistance. As Ortolani pointed out, Tenaris’s vertically integrated production model allows for tight process control at every stage—from steelmaking and casting to hot forming and final heat treatment. This integration enables the company to implement best practices and respond swiftly to evolving customer needs or regulatory changes.
“By continuously monitoring and adjusting our production parameters, we can ensure consistent microstructure formation and mechanical properties, which translate into enhanced product performance and durability,” Ortolani said. “This is especially important as power plants operate longer hours and at higher efficiencies to meet growing energy demands while reducing environmental impacts.”
In addition to manufacturing and metallurgical advances, the collaboration has also spurred innovation in quality assurance and testing. Tenaris employs a wide range of non-destructive testing (NDT) technologies and destructive testing protocols—including creep rupture tests, Charpy impact tests, and fracture toughness measurements—to verify compliance with international standards such as ASME, ASTM, and EN specifications. The insights gained through collaboration with EPRI allow Tenaris to refine these procedures and adapt them for newer material grades and more demanding operational conditions.
Beyond technical achievements, the partnership also represents a broader commitment to sustainability. As the global energy transition gathers momentum, many countries are rethinking their energy infrastructure. While renewable energy sources like wind and solar are gaining traction, thermal power remains a vital component of the energy mix, especially for grid stability and peak load management. The efficiency and environmental impact of these plants, however, depend significantly on the performance of materials used in critical systems.
By developing steels that enable higher operating temperatures and pressures, Tenaris and EPRI are supporting the deployment of ultra-supercritical (USC) and advanced ultra-supercritical (A-USC) power plants, which offer significantly improved thermal efficiencies and lower CO₂ emissions per megawatt-hour generated. These next-generation plants rely heavily on advanced materials capable of maintaining structural integrity under extreme conditions—a challenge that this partnership is helping to address.
As Tenaris continues to collaborate with EPRI and other research institutions around the world, it remains committed to investing in science, technology, and operational excellence. The goal is clear: to deliver reliable, high-performance steel solutions that meet the needs of an evolving global power industry and contribute meaningfully to the creation of a more sustainable energy future.
Through knowledge-sharing, advanced manufacturing, and proactive materials innovation, Tenaris and EPRI are not just responding to the challenges of modern power generation—they are helping to shape the solutions of tomorrow.