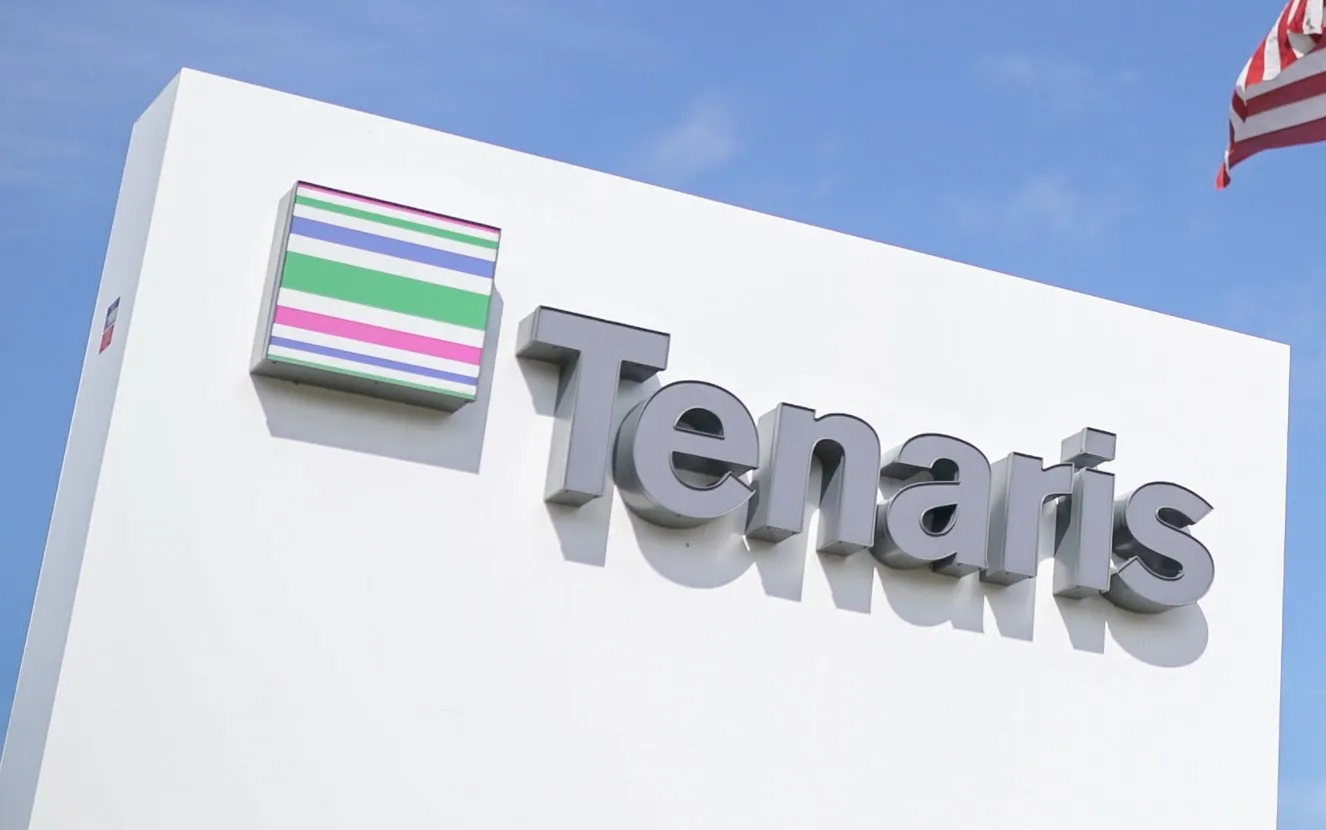
Tenaris Debuts Dopeless® Weld-On Connectors in Brazil, Completing Full Dope-Free Solution for Entire Well
Tenaris has successfully completed the installation of two casing strings featuring its advanced Dopeless® technology in Brazil’s offshore Búzios field, operated by Petrobras in the Pre-Salt region. This milestone marks the first deployment of Dopeless® technology for large-diameter weld-on connectors in the country, rounding out Tenaris’s dope-free solution portfolio for full-well applications. The successful operation not only underscores Tenaris’s longstanding leadership in sustainable oilfield solutions but also reflects its strategic focus on safety, operational efficiency, and environmental responsibility.
The first installation involved a 36-inch conductor casing string outfitted with TenarisHydril BlueDock® connectors coated with Dopeless® technology. These robust connectors were combined with automatic anti-rotational keys (AARK), a system designed to enable hands-free activation. This key innovation significantly improves safety by minimizing manual operations in the red zone, one of the most hazardous areas on the offshore rig floor.
Following the initial success, Tenaris carried out a second installation in the same offshore field a few weeks later. This phase involved the deployment of an 18-inch surface casing string, also utilizing Dopeless®-treated connectors. Both installations were supported on-site by Tenaris’s experienced Technical Sales and Field Services teams, who ensured flawless execution. The operations were completed without any issues, with zero rejects and no re-makeups—demonstrating both the reliability of the Dopeless® technology and the precision of the execution.
Expanding a Proven Technology to Large-Diameter Applications
Tenaris’s Dopeless® technology has now been successfully applied across the entire well, from conductor to production casing. This positions Tenaris as the only OCTG (Oil Country Tubular Goods) manufacturer in the world offering a truly comprehensive dope-free solution. First launched in 2003 in the challenging offshore environment of the Norwegian North Sea, Dopeless® technology was designed to eliminate the need for thread compounds—commonly known as “dope”—during storage, transportation, and installation of tubulars.
The coating is applied at the mill under tightly controlled conditions, ensuring consistency and performance in even the harshest offshore environments. Over the past two decades, Dopeless® technology has proven itself across more than 60 countries, with over 74 million feet of dope-free pipe installed globally. Its expansion into large-diameter connectors marks a new chapter in this successful journey, fulfilling the market’s growing demand for sustainable and operationally efficient solutions in high-stakes offshore drilling.
A Commitment to Safer Operations and Environmental Stewardship
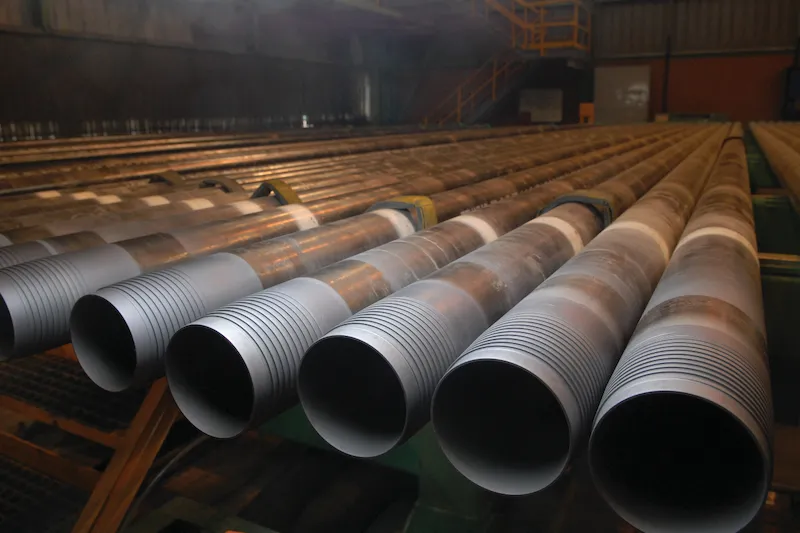
Dopeless® technology offers a multitude of benefits that go far beyond eliminating the traditional thread dope. By removing the need for on-site application and subsequent cleaning of thread compounds, the technology minimizes the environmental footprint of drilling operations. Traditional thread dope can pose a contamination risk to marine environments, and its application is labor-intensive, often requiring personnel to work in close proximity to rotating machinery and other hazardous equipment.
With Dopeless®, operators eliminate the need for this high-risk step entirely. The automatic anti-rotational keys used in conjunction with the technology further enhance this safety profile by reducing human interaction in the red zone—an area historically associated with the highest number of injuries on a rig.
Renato Catallini, President of Tenaris in Brazil, emphasized the significance of this achievement in improving both safety and sustainability. “This operation sets a new global benchmark in conductor and surface casing technology,” he said. “Our Dopeless® technology contributes to a safer red zone, one of the highest-risk areas on the offshore drill floor. The operator highlighted the significant benefits of not needing to perform manual cleaning and lubrication tasks in this area, leading to enhanced safety conditions and a reduced environmental impact.”
The adoption of Dopeless® connectors in Petrobras’s operations aligns well with the increasing focus on ESG (Environmental, Social, and Governance) practices in the energy sector. As international operators place greater emphasis on sustainability, innovations such as Dopeless® provide both practical and reputational advantages.
Twenty Years of Innovation and Field Experience
Tenaris’s leadership in dope-free technology has been built on years of rigorous product development, exhaustive field testing, and continuous customer feedback. Since its first deployment over 20 years ago, Dopeless® technology has evolved to meet the demands of increasingly complex well architectures, deeper drilling operations, and tighter regulatory standards.
Tomás Castiñeiras, Global Director of Technical Sales at Tenaris and a key figure in the original rollout of Dopeless® in Norway in 2003, reflected on the journey. “We’ve dedicated years of product development and field experience to making Dopeless® technology available for the full well. From the first application in the North Sea to this recent success in the Brazilian Pre-Salt, we’re proud to say Tenaris is the only OCTG manufacturer worldwide capable of covering the entire well with a dope-free solution.”
This ability to offer an end-to-end Dopeless® solution means operators can streamline logistics, simplify planning, and reduce variability across different casing sections. It also ensures consistent performance from top to bottom, avoiding the risks associated with mixing traditional and dope-free components in the same well.
Supporting Customers with Integrated Services
Tenaris’s success with Dopeless® in Brazil was supported by its integrated service model, which combines high-quality tubular products with expert technical assistance and real-time field support. The company’s Technical Sales and Field Service teams were embedded in the operation from the planning phase through execution, ensuring seamless alignment with Petrobras’s operational requirements and safety protocols.
These services are essential to the successful implementation of advanced technologies like Dopeless®, especially when applied in high-risk and technically challenging offshore environments. By working closely with customers, Tenaris ensures not only that its products perform as intended but also that its innovations translate into measurable gains in safety, efficiency, and sustainability.
The Future of Dope-Free Tubulars
The successful deployment of Dopeless® technology for large-diameter weld-on connectors represents a significant step forward in Tenaris’s ongoing mission to lead the energy sector toward a cleaner, safer future. As offshore drilling operations venture into deeper waters and more complex geologies, the demand for technologies that combine reliability with environmental responsibility will continue to grow.
Tenaris is already looking ahead, exploring additional innovations to further optimize the performance of Dopeless® coatings and expand their applicability to new well architectures and environments. The company’s global manufacturing and R&D footprint ensures it can respond to regional needs with tailored solutions while maintaining the consistency and quality that have become hallmarks of the Dopeless® brand.
With over two decades of proven field success and continuous development, Dopeless® technology stands as a powerful example of how sustainability and performance can go hand in hand. Its latest milestone in Brazil demonstrates Tenaris’s ability to not only deliver innovation but also to shape the future of the global energy industry—one well at a time.